Supply chain volatility is disconnecting factory operations from corporate strategy
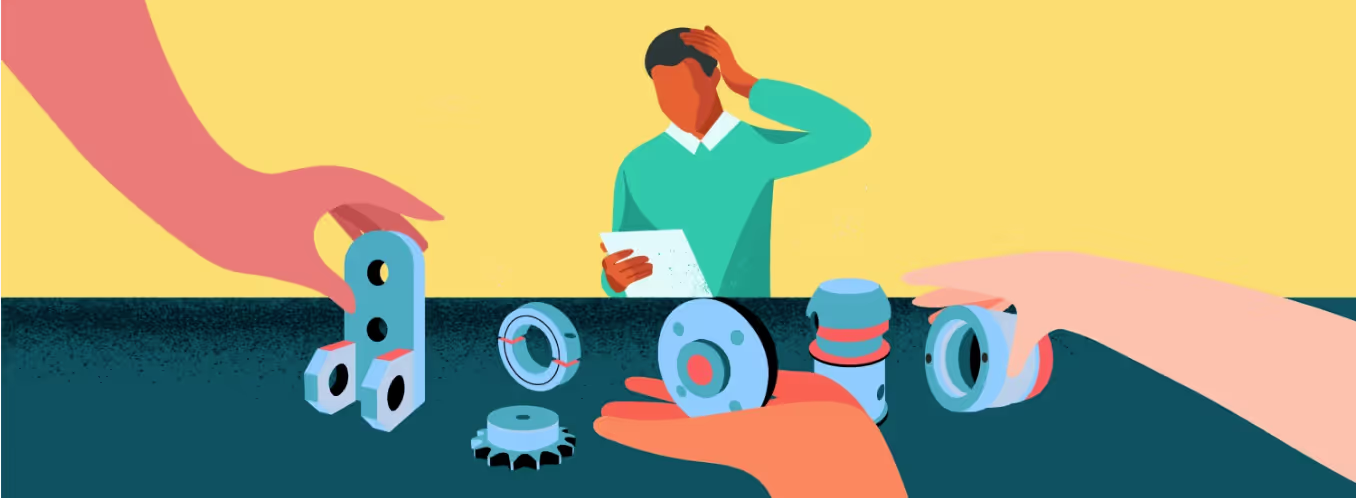
In the world of manufacturing, things can go wrong at any time. A global event can kickstart a domino effect which leads to laboratories receiving their crucial medical equipment later than planned, an airline without a key part needed to keep their fleet operating at full capacity, or end customers experiencing significant delivery delays for their new luxury watch. But it doesn’t always take a global crisis — even small events can have large ripple effects, causing disruption further down along the line.
Within factories, these types of unplanned supply chain constraints cause operational mayhem, leading to stressed staff, stop-start processes, economic dislocation, and in severe cases, temporary halts on production until the supply chain is regulated again. Supply chain constraints have been particularly significant in recent years: research shows that there were 11,642 supply chain disruptions worldwide in 2021, up from just 3,700 in 2019.
The problems for factory operations start further up the supply chain. Over 65% of supply chain managers still use Excel spreadsheets as a management tool, meaning the significant amount of data that manufacturers need in order to map out appropriate factory operation strategies is often inaccurate and unreliable.
Add in a crisis as unexpected as Covid-19, where 72% of companies reported experiencing negative effects on their supply chain—paired with a majority experiencing an increase in customer demand—and factory operations quickly descend into a nightmare.
Supply chains under pressure
If manufacturers don’t have the information they need, they are unable to run their business and deliver their products on time, at cost. According to the Global Supply Chain Pressure Index (GSCPI) — which comprehensively maps global supply chain conditions by analyzing a range of aggravating factors facing manufacturers, from Chinese and Korean delivery times, to goods and producer price inflation in the United States and Europe — factories are having to respond to changing conditions on a near-daily basis, meaning it’s almost impossible to plan operations as tightly as the industry requires. This high volatility leads to production blockers that are inherently unplanned, causing further disconnect between supply chain strategy and factory execution. While strategic, sales and operations planning take place on a monthly and annual basis, factories manage their material and capacity planning on a weekly basis, meaning strategies can become almost obsolete if conditions have changed quickly.
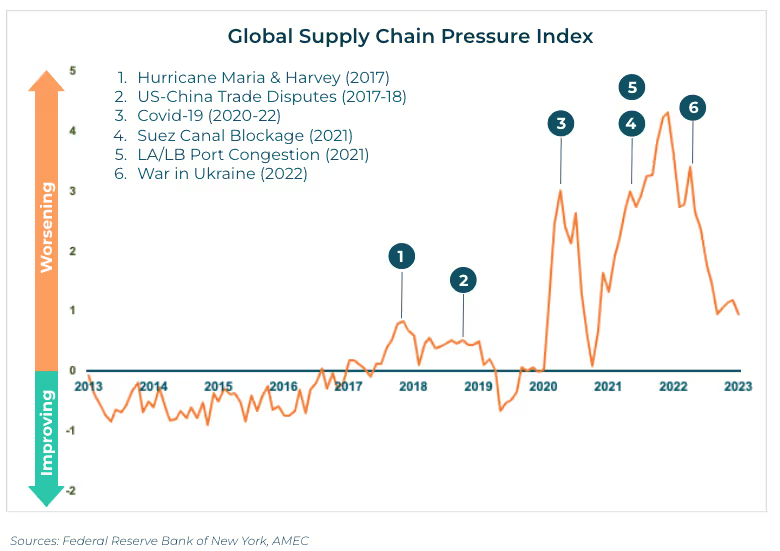
Existing tools do not provide operational teams the necessary data visibility
For decades, companies were able to successfully rely on ERPs to gain greater visibility into their planning and organize production schedules accordingly. Yet as the frequency of fluctuating variables has skyrocketed, ERPs no longer provide the agility needed for teams to reassess their planning. In response to this, teams have begun improvising by working with separate tools like Excel, creating two big problems; firstly, data becomes siloed within the organization, rendering a global overview impossible and jeopardizing the quality of the data; and, secondly, the aforementioned tools do not enable teams to act fast enough and stay a step ahead of volatility.
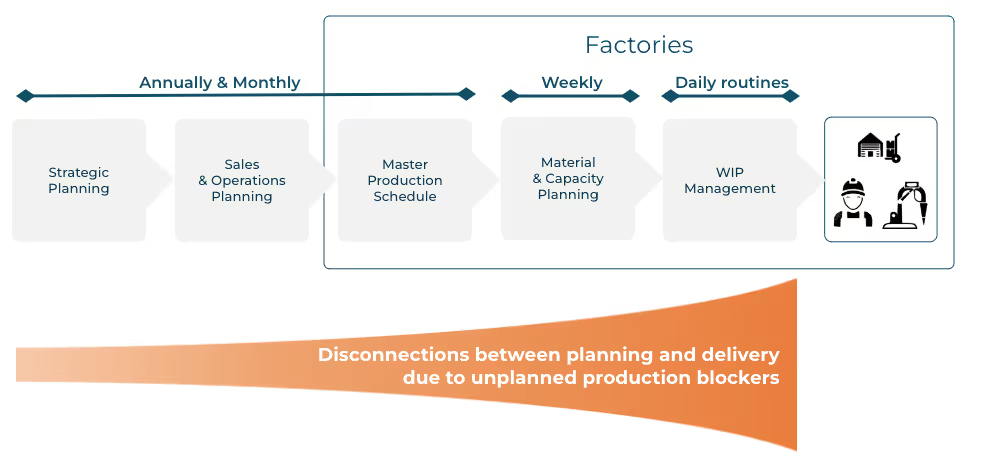
As a result, companies are no longer able to manage their supply chain performance using a centralized approach. In the current manufacturing environment, strategies set out half a year in advance are not suited to the changing supply chain landscape. As factories struggle to keep up with ever-shifting conditions, their workload increases dramatically as they juggle the day-to-day operational challenges with inaccurate long-term planning set out by corporate months prior.
The need for agility
The solution? Companies need to transfer more agility and autonomy to factories. The oil tanker and speedboat analogy comes into play here. Manufacturing giants are often compared with oil tankers: they’re sturdy and can handle huge loads, but they’re also slow and take a long time to turn around. This approach might work well in stable conditions, but when faced with challenges from every direction, companies need to be able to pivot their factory operations on a dime if they want to survive. Even a midsize company such as Made.com wasn’t agile enough to adapt to changing circumstances, and faced bankruptcy as a result. If the past three years have demonstrated anything, it is that manufacturers should leave the oil tanker approach behind and instead adopt speedboat characteristics, becoming light, agile, and able to change directions quickly when needed.
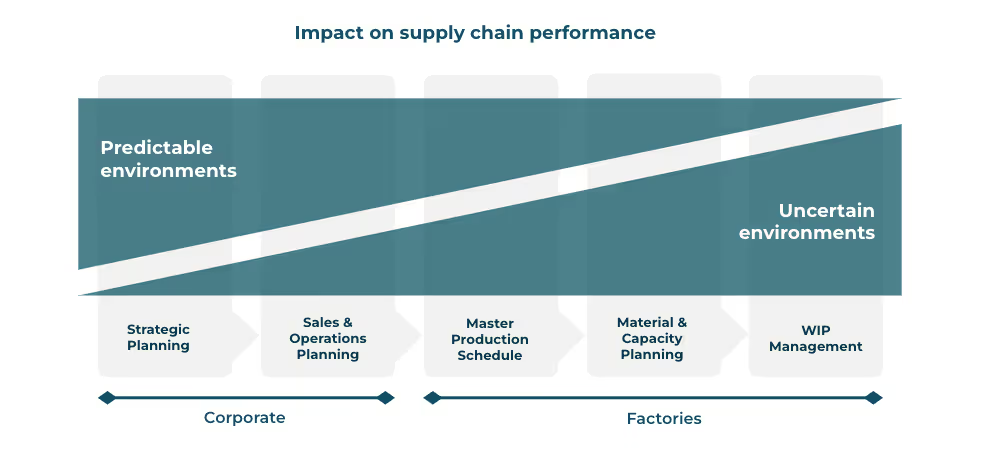
There can be no agility without accurate insight into data and processes. To better manage production blockers, many factory teams have adapted to the new reality of extreme volatility: they have implemented processes that allow them to continuously adjust to daily changing variables. In order to optimize factory operations, they’ve created processes focused on anticipation of production blockers, and then the implementation of corrective actions to mitigate the negative effects of these blockers. On a slightly longer-term scale—a weekly and monthly basis—they try to optimize production plannings by assessing its feasibility. But the efficiency of those processes has reached its limits as operational teams aren’t equipped with the right tools to act fast enough in a rapidly changing environment.
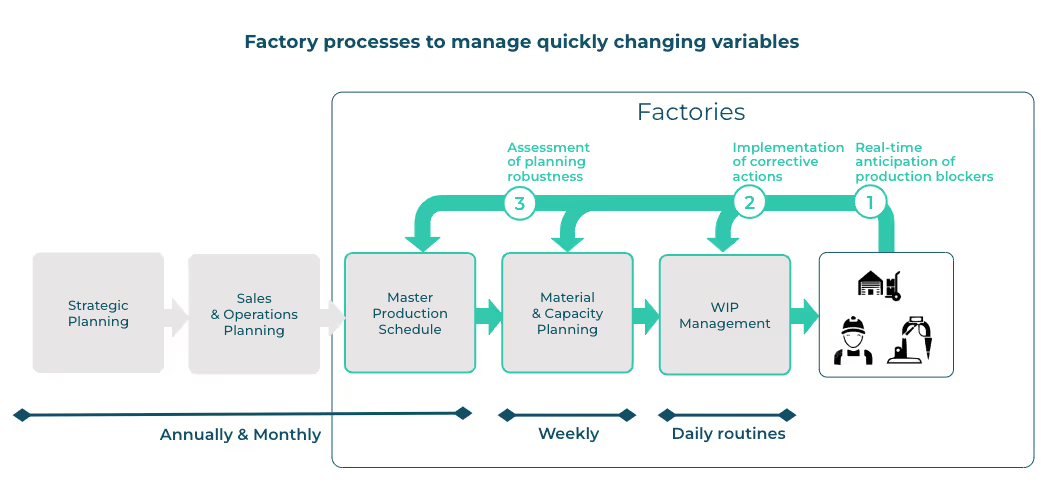
The 6 limitations of current solutions and approaches
Despite these efforts, these traditional tools and processes have reached their limits for six key reasons.
Sequential planning is obsolete
The use of sequential production planning processes means that as soon as one blocker arises, the entire process collapses, often leading to lethal operational failures down the line. Global supply chain disruptions force factory operations to adapt on a near-daily basis, rendering it impossible to pre-empt conditions to the degree required.
ERPs are no longer fit for purpose
Commonly-used Enterprise Resource Planning (ERPs) solutions are also not adapted to manage daily operations. They don’t provide the agility needed for users to run their regular analysis with quickly changing variables and to manage their daily operations.
Data is difficult to access
Due to the outdated nature of many ERPs, data and information is typically siloed, because teams need to manually export information into Excel spreadsheets. This use of shadow IT and human labor leaves too much room for human error. As a result, teams are often working with different numbers, leading to confusion for leadership that needs visibility on factory status and capacity to deliver on Master Production Schedules.
Partial data leads to misanalysis
Following on from this, gathering the data needed to assess the state of operations is a complicated process, and working with partial sets or misaligned data can lead to inaccurate conclusions. Excel and VBA also have limited computing capabilities, and are not fit for purpose, meaning teams rely on simplified analysis. Essentially, they don’t have all the information they need to make crucial business decisions when it comes to factory operations.
Teams are misaligned
Factories are a complex ecosystem involving teams across customer support, production control, engineering, material management, plant management and supply chain. Internal alignment between teams requires hundreds of emails and managerial routines, because there’s no centralized way of ensuring everyone is working with the same information. This is especially true in multi-level BOM production scheduling, because it requires the alignment of the sequencing and material capacity for multiple production lines or teams—sometimes in plants in different areas or countries— in order to get to the right sequence to re-adapt optimally to demand. The impact? Painful and ineffective collaboration that leaves room for unnecessary misunderstandings and errors across the board.
Factory operations teams are constantly firefighting
This all leads to chaos in factory operations, which in turn creates a heavy emotional and cognitive burden for those operations teams. They’re dealing with stress and frustration because they lack the right tools to handle volatility, and they’re constantly firefighting rather than working on value-added tasks. As a result, they spend most of their time chasing data instead of focusing their energy and skill-set on the tasks they were hired to do.
Constant fire fighting has a toll on the overall business
Supply chain constraints pose considerable challenges for factory operations—but what about the wider impacts on the business itself? Unsurprisingly, haphazard factory operations (through no fault of their own) present significant negative impacts for the business as a whole, including delivery delays, incomplete or unrealistic forecasts, and costly last minute solutions. It’s clear that urgent change is needed to allow factory operations to better respond to supply chain constraints—for the wider business, for the end customer, and for the employees themselves.