3 Reasons Why Manufacturing Operations Are More Complex Than Ever (And Will It Be Simpler When Covid Is Over?)
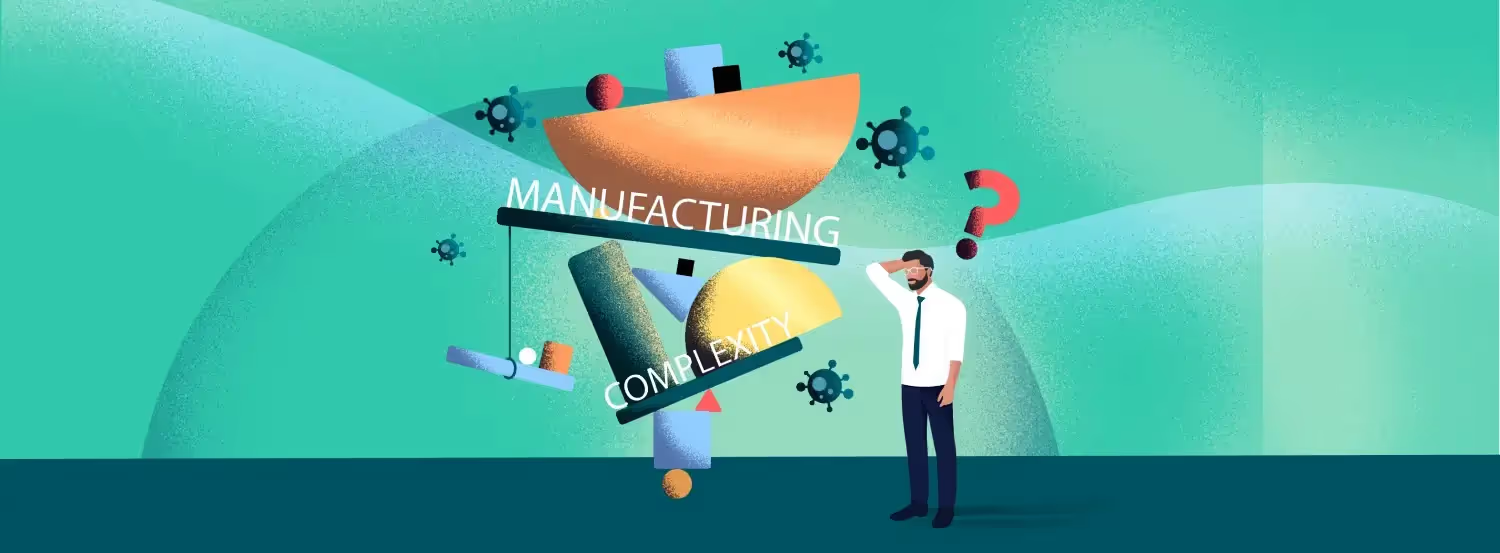
At the time we are writing this paper, a shortage of critical raw materials is causing such a disruption to the global manufacturing industry that it’s making headlines worldwide.
The dearth of raw materials that is bringing whole industries to a standstill is just one of the challenges manufacturers have to deal with in the aftermath of the COVID-19 crisis.
As a matter of fact, the pandemic has amplified long standing trends and factors of disruption, thus exacerbating the complexity of manufacturing operations and supply chain management.
Let’s explore the forces of disruption that are currently transforming the management of industrial operations and supply chains.
1. The Ripple Effect Of The Crisis
Let’s first face the elephant in the room: the COVID-19 crisis, which caught all organizations by surprise. The wave of lockdowns compelled consumers to turn to digital channels and to change their buying behaviors dramatically in a matter of days. Some businesses had their work cut out for them to meet spiking demand for essential products. Others were left with bulging inventory. Meanwhile, organizations had to face sudden workforce constraints and delays in supply and transport. Long story short, both customer demand and supply delivery suddenly became utterly unpredictable.
The brunt of the crisis now seems to be behind us. But manufacturers are not out of the woods yet. For one thing, restoring normalcy takes time. According to a Capgemini research report, about 70% of organizations have taken more than three months to re-establish operations.
What more, pent-up demand is placing further strain on already stretched supply chains. Growing backlogs in global supply chains seem unlikely to be fixed anytime soon.
Last but not least, the overall market uncertainty we’re currently witnessing seems to be here to stay, even as the world emerges from the pandemic. Customers — both consumers and corporations — are still adjusting their consumption and usage patterns to the new (ab)normal. There is still a huge question mark hanging on the future of remote working, of traveling habits, and more.
Amidst heightened levels of volatility in demand, everything indicates that global manufacturers need to get used to navigating exacerbated complexity.
2. The Innovation Imperative
The pandemic didn’t create customer demand volatility. It revealed and exacerbated pre-existing trends. In fact the pace of demand change has been accelerating for years now.
Reasons for fast-changing market expectations include heightened global competition and increased customer choices, rapid technology improvements and faster product obsolescence, increased consumer consideration for an ever-growing range of product- and non-product attributes (such as Corporate Social Responsibility and brand image). In fact, the past few months saw a number of new, greener products mushroom — from insects-based food products to virtual fashion, from electric vertical take-off and landing (eVTOL) aircrafts to hydrogen-fuelled fleets of commercial vehicles, and more. As these alternative offerings are gaining traction, they have the potential to upend markets.
Accelerated change in market expectations translates into growing consumer impatience and therefore into shorter delivery windows. Today’s consumers don’t want to “Buy it now”, they want to “Get it now”. Because they have never had that many options, their tolerance for friction and delay is at an all-time low. And that impatience is now spreading to the business world: as decision-makers got used to effortless order tracking and next-day delivery from Amazon, they have grown to expect the same speed and transparency when ordering complex machinery in their professional functions.
That’s a new fact of life for manufacturers: customers are now setting the pace. Vendors have to keep up and adjust operations and supply chain management accordingly. Accelerating product development and improvement cycles and evolving management practices with a focus on speed and agility is becoming a matter of business survival. Today more than ever, hesitation and delay can be fatal.
In a context of global shortages, this may require veering away from just-in-time manufacturing processes and accepting higher inventory to ensure ability to meet demand. The need for speed is also prompting many businesses to produce and ship closer to the customer. Still according to CapGemini, 65% of organizations are now investing in localizing their supplier and manufacturing base.
3. From Mass Production To “Me” Production
Not only are today’s consumers more fickle in their expectations and more impatient, but they also demand highly personalized experiences and products. We are a very long way from Ford’s “Any colour - so long as it's black”. Digitally and socially connected buyers want products and services that are tailored to their unique lifestyles and preferences.
This is yet another factor of complexity. Lest they risk losing their clients to the competition, manufacturers have to offer an increasing variety of products, in lower volumes, and to deliver faster on more customized orders. This is a game-changer for incumbent businesses that based their model on production of one-size-fits-all products in large batches.
This means that manufacturers need to keep track of a wider mix of products with more stock keeping units — and therefore of an expanded list of parts and components — with different lead times and different tools and machinery involved. This also means that operational teams have to juggle more multi-level bills of materials, more processes and more quality standards, adding to the complexity.
As the management of day-to-day operations increases in complexity it becomes crucial to gain visibility into material availability and to adjust production and delivery cycles to accommodate smaller, diversified baskets.
When it comes to production strategies, consumer appetite for hyper-customization warrants a shift from a make-to-stock to a demand-driven, make-to-order approach — where supply chains allow it. In a nutshell, the whole supply chain needs to be rethought to meet the challenges of the new world.
Need A Little Help..?
In a deeply uncertain and volatile business landscape, it is mission-critical for manufacturers worldwide to improve the resilience and agility of their operations. The best path towards business agility is digitalization.
First of all, you can’t manage what you can’t see. In a traditional plant setup, key information is scattered across email threads and contextual systems. The resulting blind spots and information silos across teams and departments have been hampering the efficiency of industrial operations. Industry players need digitally-enabled solutions that provide end-to-end visibility and transparency to supply chains and operations in order to align the plant on a common vision.
Enabling data-sharing between internal teams (for example between production and planning teams) and across partner ecosystems (e.g. suppliers, subcontractors, distributors) also goes a long way towards stimulating effective collaboration. New digital solutions provide manufacturers with collaboration- and communication-oriented capabilities to accelerate interactions, to fight the proliferation of scattered spreadsheets and email threads, and to streamline information flows and such processes as problem escalation.
Optimizing the escalation process is good. Limiting the need for escalation altogether is better still. With the support of advanced analytics and intelligent simulation capabilities, manufacturers can monitor an expanded range of risk factors and anticipate roadblocks ahead of time. The ability to run ‘what-if’ scenarios and test possible courses of action will not only help them to respond more rapidly to disruption, but also increase overall reliability of planning activities.
Ideally, manufacturers should be able to leverage both operational data and enterprise data to support daily decision making in Supply Chain and Operations management. Data management has already become a core supply chain activity and can provide a competitive advantage for manufacturers.
Finally, businesses should make sure that the digital tools they invest in offer user-friendly, consumer-like experiences to their team. This is a prerequisite to enterprise-wide adoption and to realizing the true ROI of technology investments.