Are you firefighting in your plant? Here is how you can empower teams to harness complex operations
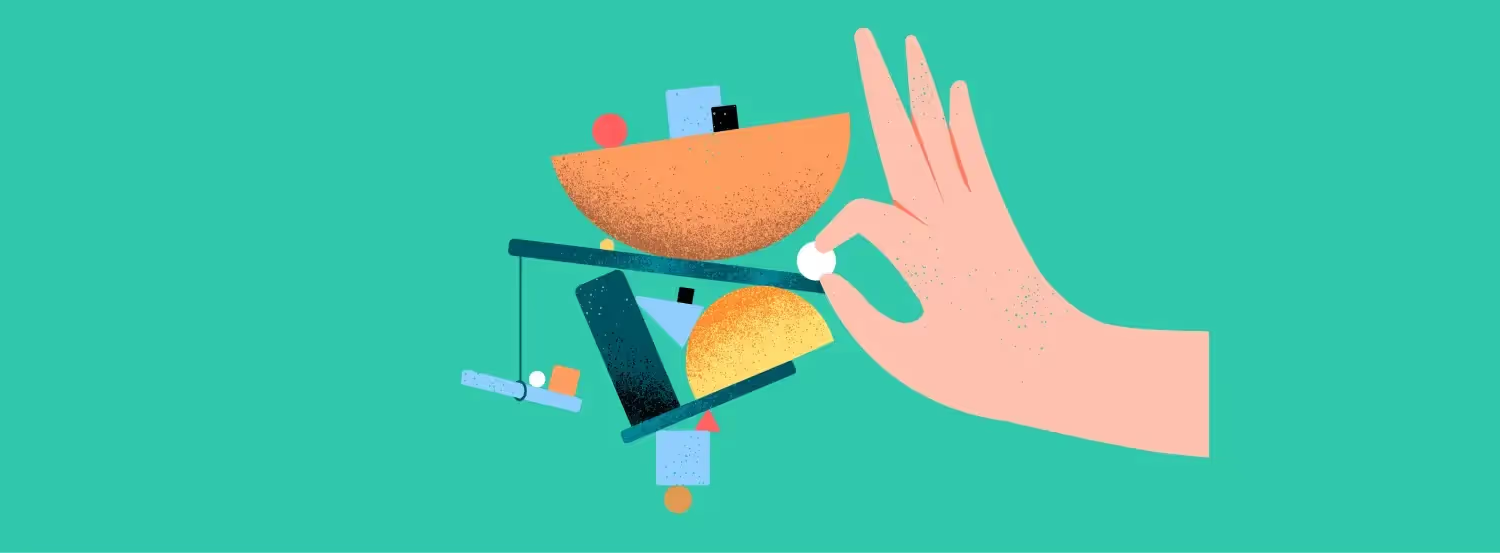
Anyone with work experience in a plant knows it: things often look and feel out of control. The typical production worker is in constant firefighting mode, with little to no visibility into what’s coming next.
That’s chiefly because the teams dedicated to production control usually don’t have what it takes to manage the complexity at hand. They simply lack the data capabilities to coordinate and process the huge number of variables involved in the production process and anticipate hurdles in time.
This is about to change. With the advent of Operational Intelligence for manufacturing, production control teams are now empowered to get the priorities right and turn the plant into a well-oiled machine that delivers consistently.
Production control challenges at a glance
What’s the end goal in industrial production? In a nutshell, to deliver the on-time, on-cost, on-quality products that clients expect."
To ensure that nothing comes to block operations and jeopardize delivery, production control teams are required to coordinate a whole raft of parameters. From the inbound customer order to the final outbound shipment, the sheer range of factors to manage is humbling. They need to make sure that the right parts and the resources with the right skills are available at the right time. That the due maintenance operations are performed to keep equipment in working order, but that maintenance work doesn't clash with scheduled production operations. That each workstation completes tasks in the allotted time.
Considering the scale of operations, something is bound to go wrong at some point. This is why a key responsibility of production controllers is to anticipate production blockers — such as delay in supplier delivery, machine downtime, unavailability of critical resources, or scheduling conflicts — and to figure out a way to solve or work around the issues in a timely manner. Controllers need to make sure that diverse teams are on the same page and that each is aware of any event that may impact their own work.
The cost of poor anticipation
What happens when production controllers are unable to fully play their role as binding agents? Production teams stumble across the problems at the last minute, which makes it all the harder to find fixes. They’ll discover at the very last moment that the measuring device they need is actually unusable because calibration wasn’t performed as scheduled, or that the parts that were supposed to be delivered were not.
When faced with such unanticipated hurdles, production workers typically spend huge amounts of time trying to figure out the causes of the problems and find ways to solve them. They’ll have to find a fix in urgency and scramble to put together a plan B — which is usually not the next best option.
That directly translates into productivity loss. Having skilled workers spend 60 to 70% of their time on low-value information gathering is an obvious waste of productive resources, with impact on the bottomline. Moreover, workers in constant firefighting mode may end up stressed and demoralized, causing lower employee engagement, reduced work performance or even high turnover.
To the costs of poor productivity, add the cost of sub-optimal decisions made in urgency (for example a higher-than-average scrap rate, or subpar resource allocation) and the cost of urgency itself: worker overtime and cab fares to make up for lost productivity, express shipping to mitigate delay… Those usually don’t come cheap.”
Even more critically, improperly addressed production blockers may prevent the plant from meeting client commitments altogether. Chief among the consequences is obviously the loss of revenue. In the best case scenario, you will incur penalty for delayed delivery. That is, if the order is not simply cancelled. In any case, you’ll be leaving money on the table and fail to meet your target revenue. In addition to the short-term impact on the bottomline, a track record of missed deadlines can hurt the goodwill and market reputation of the company, jeopardizing its very future.
We’re not talking theoretical worst case scenarios. It is all too common to see a workshop manager realize at the eleventh hour that a large customer order cannot be processed in time because a delay in supplier delivery was not properly accounted for. Or, conversely, that a supposedly late supplier shipment actually made it through in time — which would have enabled to salvage a customer order if only the right person had been notified.
Faced with such severe consequences, why don’t plants tighten their grip on operations? That’s actually a haunting question for many top executives in the industry. They’re usually not on the plant floor. When learning that a million-dollar client delivery was missed they’ll often ask: What the heck is my production control team doing?
An alignment problem
Unfortunately, it’s not that simple. At all. Several layers of information asymmetry are conspiring to make production opaque and intricate.
For one, a multiplicity of disconnected stakeholders. Although their actions are interdependent, the various teams involved across the value chain — Operations, Supply Chain, Engineering, Customer Relations — tend to work in silos. Each will use their own process, and sometimes their own system of record. What more, they hardly even speak the same language: when asked about a production order, a Supply Chain manager will typically respond in terms of purchase order. Accordingly, just assessing the impact of a change in a sales order on the production and purchasing activities requires the various teams to get together, retrieve and share the right data, discuss at length to find an understanding. And getting them to align and focus their effort towards the same goals is yet another matter.
What more, you’re dealing with a complex ecosystem of scattered suppliers. The bill of materials for a specific deliverable typically lists hundreds of components sourced from various suppliers across the world. When your ability to produce within deadline is contingent on timely delivery of bolts from Hamburg, rivets from Toronto and pistons from Nagoya, how do you make sure that both Supply Chain and Production teams have the visibility they need to ensure that the right parts are available at the right time?
To top it all off, there are those occasions where you are your own supplier and your own client. Instead of sourcing critical parts from the outside, manufacturers may produce key intermediate goods themselves — which reinforces the necessity of seamless communication and collaboration between Supply Chain and Production teams.
Now, consider that puzzle at the scale of a plant with hundreds of employees, managing hundreds of operations and processes across hundreds of parts and deliverables. As a production controller, how do you reconcile the fragments into a coherent image? The human brain just can’t embrace that kind of complexity. Production is virtually impossible to coordinate without the support of a dedicated solution.
Solutions that don’t solve much
Traditionally, plants have relied on spreadsheets to monitor production. It should come as no surprise that collections of team-specific documents with very limited collaboration and consolidation capabilities don’t solve the alignment problem.
More recently, some manufacturers have acquired focused software to help manage targeted activities. They typically end up with a maintenance system, a tool dedicated to tracking missing parts, a SRM, a CRM. Which is well and good, but still doesn’t provide a cure. Information is still siloed and scattered. Getting a handle on production status still requires spending hours in meetings, dealing with a backlog of emails, reconciling information. Multiple transactional systems fail to connect the dots and align the various teams around the most pressing issues at the plant level.
True, a HR ERP module will help you make sure that a whole department doesn’t go on leave at the same time. But it won’t tell you that a worker with critical skills has to be there at a given time to perform an operation that only he or she is able to complete.
Long story short: the solutions in use so far do not eliminate the information gaps, silos and asymmetries that cost time, productivity and dollars to plants.
Pelico: connecting the dots
What production controllers need is a solution consolidating all that localized intelligence to provide a cross-team, cross-domain view. They need smart analysis capabilities to make sense out of the data, to pinpoint and flag issues — both actual and potential. They also need a platform enabling collaborative problem-solving in order to bring everyone around the optimal solution. That’s Pelico.
1. Unified operational data
Our Operational Intelligence solution empowers production control teams to cut through the fog of uncertain operations and achieve predictable outputs. Acting as an intelligent layer that sits on top of transactional systems (ERP, PLM, Time Tracking…), it reconstitutes a digital twin for operations.
2. Smart prioritization & AI-assisted recommendations
An AI engine crunches the data to detect and anticipate issues and provides insights for smart prioritization: by associating ROI calculations and impact assessment to each production blocker, it helps focus users on the most valuable actions. It will also suggest the next best action to be taken to achieve the plant’s objectives.
3. Cross-functional team collaboration
Among the most valuable capabilities for production control is a Collaborative Simulation framework that enables to simulate the plant-level impact of a variation in the sourcing or production plan and to refine it iteratively across teams. In a similar vein, the solution’s escalation engine lets users create tickets at the push of a button in order to flag up a specific issue and request the intervention of the manager in charge.
4. Measurable results
On average, our customers have recorded a 17% increase in planning adherence, a 40% reduction in missing parts, and a 15% jump in coverage rate of work orders in the first three months.”
All that in a user-friendly environment delivering the seamless, almost playful experience that today’s smartphone users have grown to expect from technology.
The bottom line? Pelico absorbs the complexity, putting production controllers in actual control of operations.