Why is it So Hard to Manage Factory Operations?
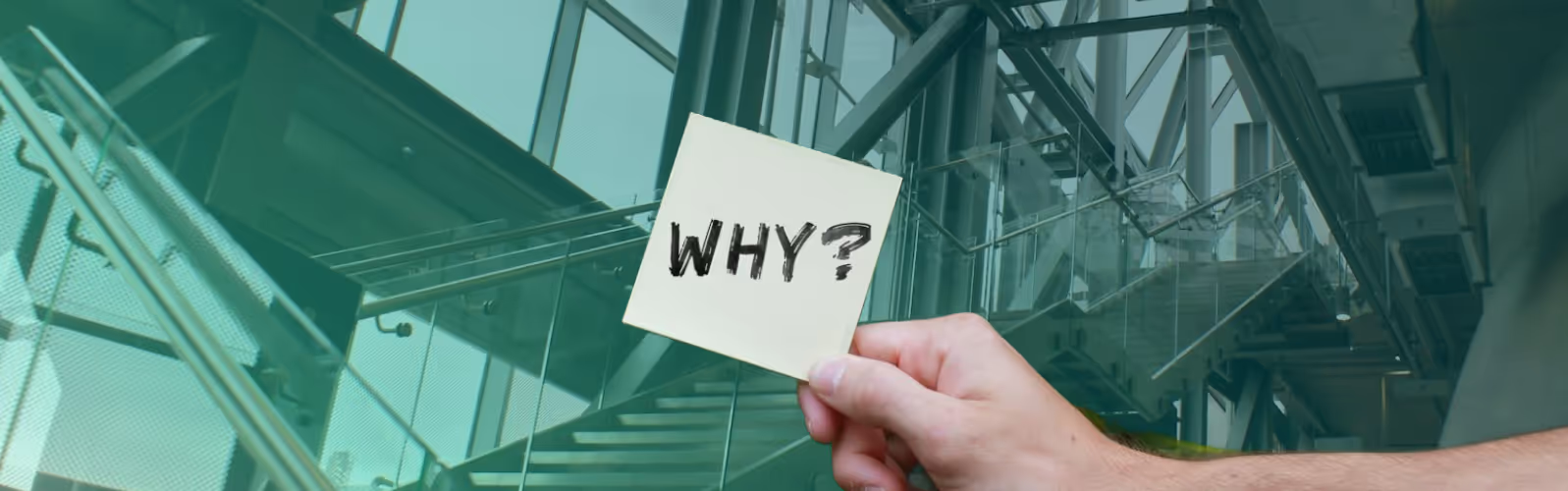
Globally, organizations lose up to 42% of one year's EBITDA due to supply chain disruptions —average per decade.
-McKinsey
Imagine a world where factory operations run with the precision of a Swiss watch—unfortunately, that’s not our reality.
On average, organizations lose up to 42% of one year's EBITDA due to supply chain disruptions per decade (McKinsey & Company ). So, why are factory operations still so challenging to manage?
Here’s our take, inspired by our daily conversations with discrete manufacturing leaders.
Defining the Optimal Factory Operations Management
Optimally managing factory operations involves a strategic and comprehensive approach to overseeing manufacturing processes that maximize efficiency, ensure high product quality, and meet delivery commitments.
While the concept of optimal factory operations management cannot be universally defined to fit all industries and maturity levels, our extensive experience in factory operations and daily interactions with users of the Pelico platform have identified several key components central to this approach:
- Disruption Management: Proactively anticipating, responding to, and mitigating disruptions such as equipment failures and supply chain delays.
- Profitability: Optimizing resource use, reducing costs, and enhancing production output to improve the bottom line.
- Leveraging Data: Utilizing advanced analytics, IoT technology, and real-time data integration to gain insights, predict issues, and make informed decisions.
- Utilizing Technology: Leveraging advanced technologies like supply chain ops management platform, enterprise resource planning (ERP) systems, manufacturing execution systems (MES), and industrial automation to streamline operations and enable data-driven decision-making.
- Customer Satisfaction: Ensuring high-quality production and timely delivery to meet and exceed customer expectations.
Disruption Management
Shocks lasting a month or more occur every 3.7 years
-McKinsey
Shocks lasting a month or more occur every 3.7 years (McKinsey). According to one of a recent analysis, companies face a supply chain disruption every 16 minutes.
Optimal management necessitates proactive and effective strategies to anticipate, respond to, and mitigate potential disruptions such as equipment breakdowns, supply chain delays, or labor shortages. If one wants to manage its factory operations optimally, they have to maintain continuous production and reduce downtime, and to do so, managing disruption is a must.
Profitability Creation and Protection
29% of businesses say they have seen a profitability or performance gain of at least 11 percent from investments in data 29% and analytics.
- KPMG
Over the course of a decade, companies can expect disruptions to erase half a year’s worth of profits or more (McKinsey). In this context, profitability is an existential imperative, not just a metric. Organizations must optimize their factory operations for maximum profitability to avoid being outmaneuvered by leaner, more efficient rivals.
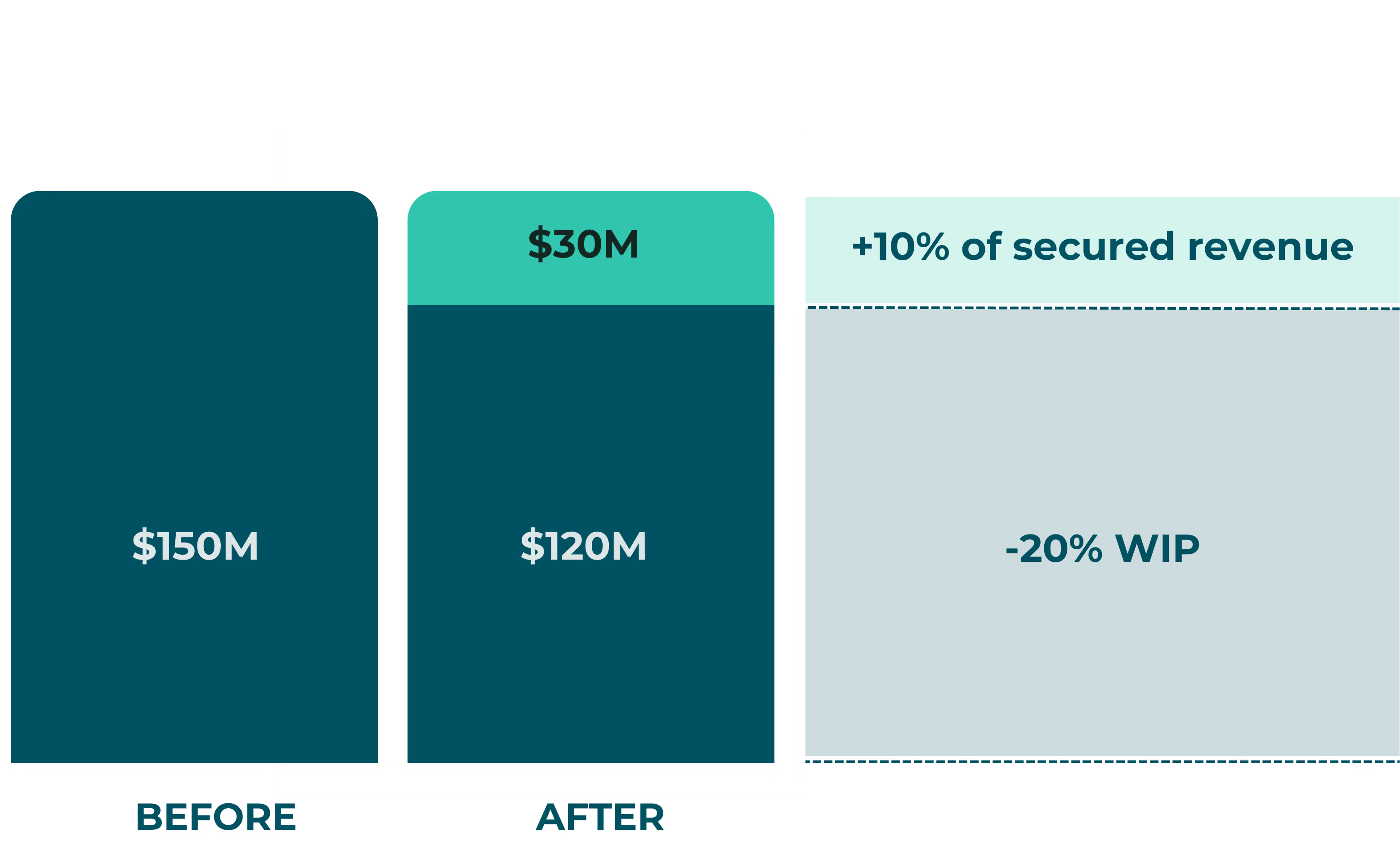
Leveraging Data
Companies that prioritize data see a remarkable 5.32% average annual increase in revenue due to their adept use of data.
-Forbes
The cornerstone of optimal factory operations management is the strategic use of data and advanced analytics, but also real-time data integration. According to a study reported by Forbes, companies that prioritize data see a remarkable 5.32% average annual increase in revenue due to their adept use of data.
This statistic underscores the tangible benefits that a well-crafted data strategy can deliver to businesses and organizations. It's not merely about data collection; it's about unlocking the power of data to enhance overall business performance. It’s notably a topic of interest for Safran Cabin.
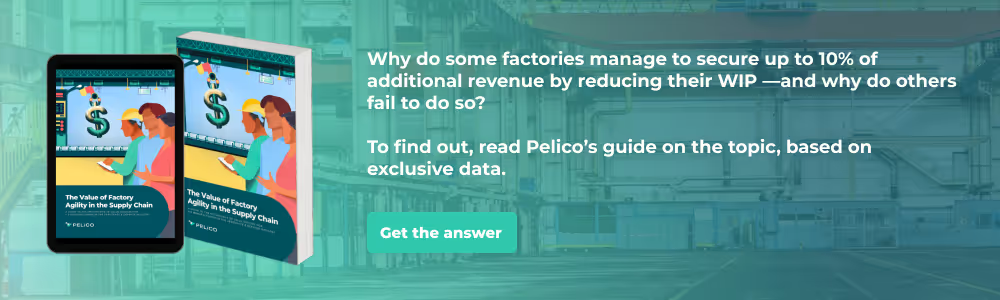
Utilizing Technology
For organizations to empower employees to work in new ways, digitizing tools and processes can significantly support success. A recent survey identified three critical changes as keys to successful transformation: adopting digital tools to make information more accessible across the organization, implementing digital self-serve technologies, and modifying standard operating procedures to include new technologies. These changes more than double the likelihood of a successful transformation. (McKinsey)
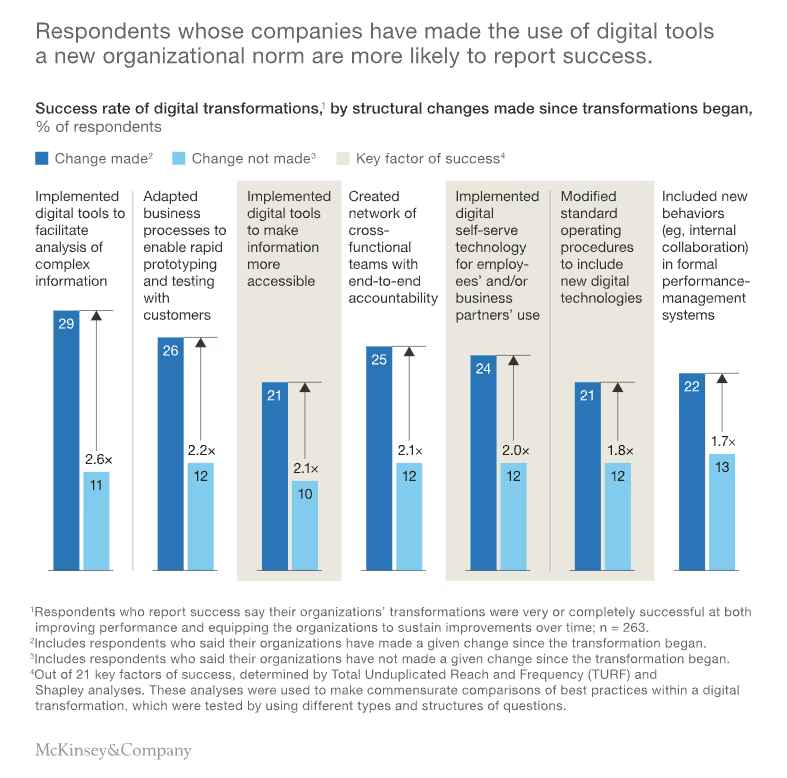
Customer Satisfaction
Ensuring that products are manufactured to high standards and delivered on schedule is paramount for maintaining and enhancing customer satisfaction.
Optimal factory management not only aligns production processes with customer expectations but also employs flexible production techniques, robust quality control measures, and streamlined cross-team collaboration.
Research underscores the importance of delivery performance in driving customer satisfaction (Lee and Joshi). Furthermore, there is a highly positive and significant relationship between customer satisfaction and customer loyalty (Mägi & Singh) indicating that higher customer satisfaction leads to greater customer loyalty.
This customer-centric approach is exemplified by Sammy Yassine, MRO Shop Director at Safran Cabin. Over the course of a webinar co-hosted by Safran Cabin and Pelico, Yassine emphasizes the importance of maintaining a strong on-time delivery (OTD) performance to prioritize customer satisfaction and loyalty.
Understanding the Underlying Complexity Factors
Factory operations are a complex ballet of moving parts, where even a slight misstep can lead to significant disruptions.
One of the vivid illustrations of this lies in the almost 45% of one year’s profits over the course of a decade that companies can expect to lose from supply chain disruptions (McKinsey).
These challenges stem from both direct disruptors, such as equipment failures, and external disruptors, like global supply chain interruptions, which are exacerbated by the inherent complexity of modern manufacturing environments.
Looking at recent market insights, we can easily see how challenging the daily hurdles faced by industry managers can be.
- More than 76% of the surveyed feel completely ready to lead through potential disruptions, and nearly 80% are completely confident their organizations could quickly adapt and pivot, if needed. (Deloitte 2021 Global Resilience Report).
- Additionally, factory operations management has faced a 4.2% rise in labor costs over the past 12 months, placing additional pressure on already thinning margins (Bureau of Labor Statistics).
Tools and Systems
Data quality is directly linked to the quality of decision making.
Melody Chien, Senior Director Analyst
Gartner
Despite advancements in technology, many factories still rely on outdated tools that fail to meet the demands of dynamic market conditions. Traditional ERP and MES systems often cannot handle the agility required in today's fast-paced environment. Gartner reports high error rates in tools like spreadsheets, which are still widely used for critical tasks, significantly affecting operational efficiency (Gartner). There is a pressing need for systems that integrate real-time data analytics and AI to predict and manage potential disruptions more effectively.
Every year, poor data quality costs organizations an average of $12.9 million. Apart from the immediate impact on revenue, over the long term, poor quality data increases the complexity of data ecosystems and leads to poor decision making.
Operational Inflexibility
Traditional factory setups often struggle with rigidity in their operations, making it difficult to adapt to sudden changes in demand or supply. This inflexibility can lead to delayed reaction times and missed opportunities. For example, companies that adopt advanced digital tools for real-time monitoring and predictive maintenance can reduce the risk of operational interruptions by up to 4 to 10% (McKinsey Digital Manufacturing, "Unlocking success in digital transformations"). Implementing more flexible operational systems can drastically improve a factory's ability to respond to market conditions swiftly and efficiently.
Economic and Human Impact
The economic impact of operational inefficiencies is profound, with increased costs and lost revenue being just the tip of the iceberg.
Moreover, there is a critical human element. Improved operational systems reduce the strain on workers, leading to better job satisfaction and talent retention, which in turn enhances productivity and innovation.
In the past, I spent a lot of time updating Excel files, but now Pelico saves me a huge amount of time so I can focus on tasks with real added value.
Charlotte Issartel , MRO Master Planner
Safran Transmission Systems
On top of this, it’s worth mentioning that organizations [implementing several complementary digital solutions, e.g.: real-time data and solutions for enhanced decision-making, RFID tagging, blockchain traceability, automated part logistics using robotics, new ERP], help them reduce warranty incidents by 50 percent, increase its flexibility to deal with its many vehicle configurations, and reduce manufacturing costs by more than 10 percent.
Striving Towards Optimal Factory Operations Management: Why Now?
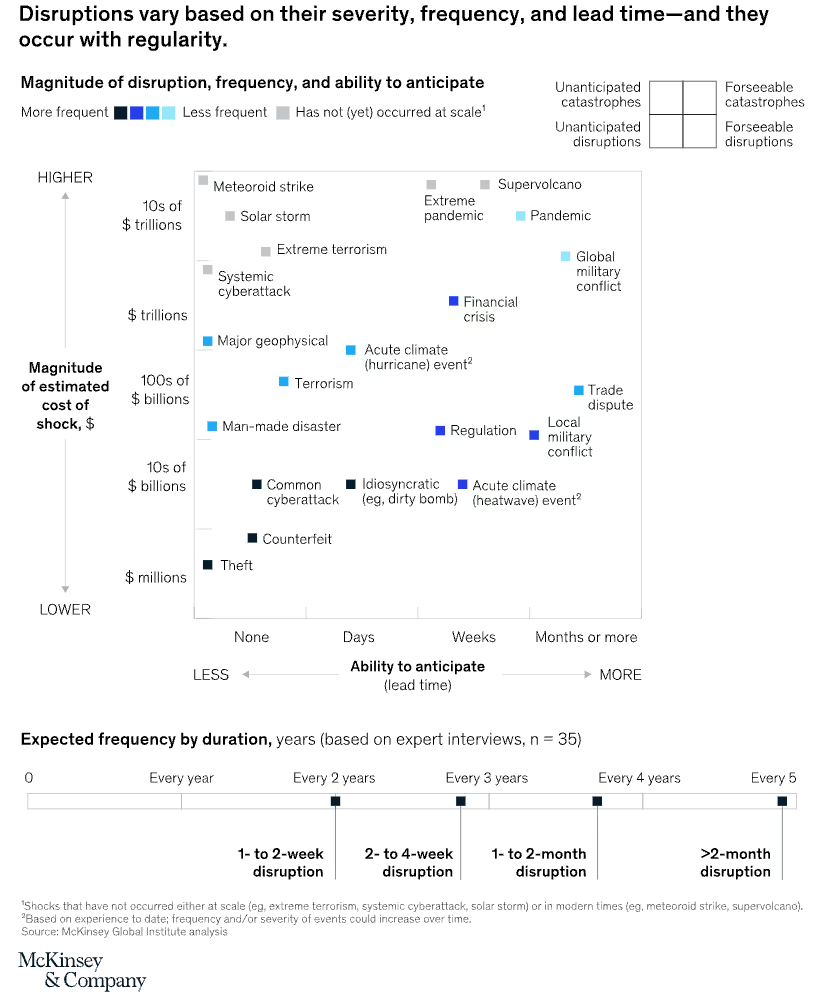
The question is no longer, "Why should I do it?" but rather, "How much money am I losing due to suboptimal factory operations management, or lack of agility?"
The pursuit of optimal factory operations is now a critical necessity for manufacturers due to intense global competition, stringent quality standards, demands for agility, rising costs, and sustainability pressures. Leveraging advanced technologies like automation, IoT, and data analytics provides powerful tools to achieve unprecedented operational visibility, efficiency, and optimization.
If we need to advocate for taking action rather than waiting, we can highlight three critical points:
- Economic Challenges of Inaction: Factories that fail to enhance their agility face significant economic challenges. Supply chain disruptions, for instance, can cause losses equivalent to 42% of a year’s EBITDA on average over a decade
.
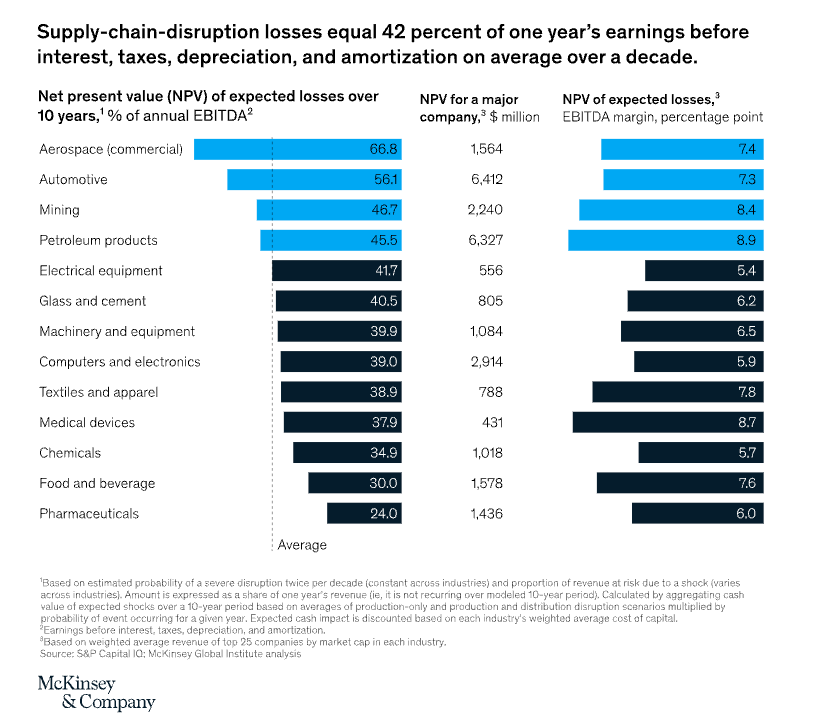
- Inefficiencies of Traditional Tools: Traditional tools and processes often fall short, leading to inefficiencies and increased costs. Due to time-consuming processes and inaccurate data, a sample plant could fail to save over 61 hours per day
.
- Substantial Cost Savings: While the journey is challenging, the rewards of optimal factory operations make the effort worthwhile. Advanced factory operations management platforms can lead to substantial cost savings. A sample plant with $300 million in revenue reported savings exceeding $16.5 million, with 49.7% of these savings attributed to decreased labor costs.
Additionally, improving factory agility not only enhances profitability but also significantly boosts customer satisfaction and talent retention, which are vital for long-term success.
Enhancing Agility to Better Manage Factory Operations: A Path Forward
The journey towards optimal factory operations management may be tough, but the rewards are too sweet to ignore.
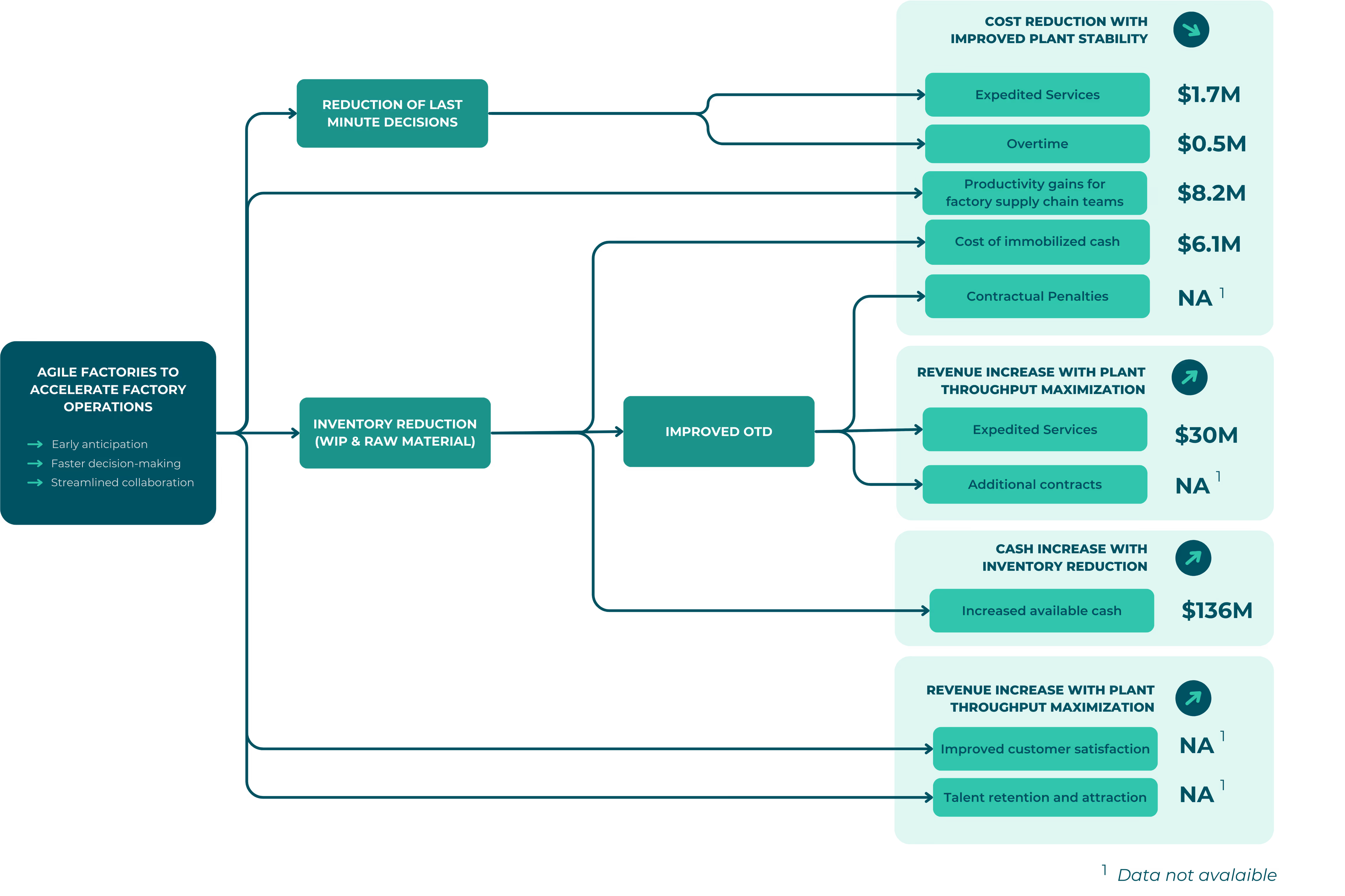
By taking a proactive approach and investing in the right strategies, technologies, and talent, manufacturers can pave the way for a more efficient, sustainable, and prosperous future for their businesses and the industry as a whole.
To tackle these challenges head-on, factories need to supercharge their operational agility. This means embracing platforms that streamline data collection, turbocharge real-time decision-making, and spark cross-functional collaboration. A recent analysis showed that factories using Pelico's supply chain operations platform enjoyed a fivefold increase in decision-making speed and an 80% boost in data preparation productivity.
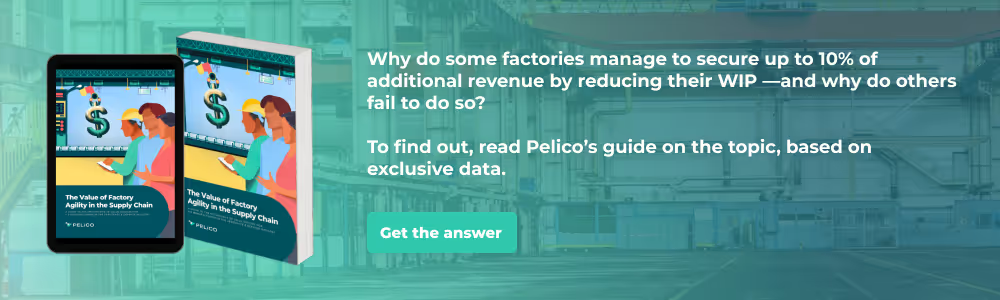