The different types of costs in manufacturing
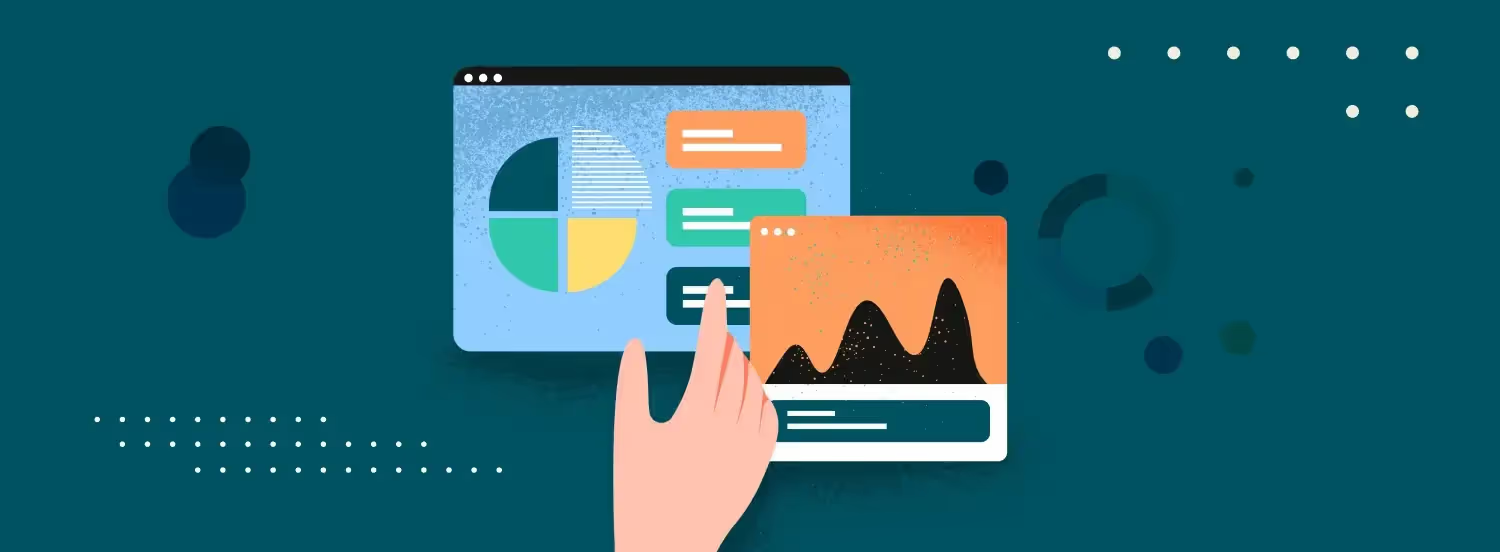
Manufacturing is the process of transforming raw materials into finished goods for sale. In this process, different types of costs are incurred. These costs are essential to consider as they impact the profitability of a business. Therefore, understanding the different types of costs in manufacturing is crucial for any business owner or manager. This article aims to explain what manufacturing costs are, the various types of manufacturing costs, the formula for calculating manufacturing costs, and why understanding manufacturing costs is important.
What is manufacturing cost?
Manufacturing cost refers to all the expenses incurred in the production of goods. These expenses include direct costs, such as the cost of raw materials and labor, and indirect costs, such as rent, utilities, and administrative expenses. Understanding manufacturing cost is crucial for a business as it helps in determining the selling price of the finished product, which in turn determines the profitability of the business.
What are the different types of manufacturing cost?
There are three main types of manufacturing costs: direct materials, direct labor, and manufacturing overhead.
Direct Materials
Direct materials are the raw materials that are directly used in the production process. These include any materials that can be traced back to the finished product, such as wood, steel, and plastic. The cost of direct materials includes the purchase price, shipping and handling costs, and any other expenses associated with acquiring the materials.
Direct Labor
Direct labor refers to the wages and benefits paid to the workers who directly contribute to the production of goods. This includes wages, salaries, and benefits paid to production workers, supervisors, and quality control personnel. The cost of direct labor is determined by multiplying the number of hours worked by the hourly rate.
Manufacturing Overhead
Manufacturing overhead includes all other costs associated with the production process that cannot be directly traced to a finished product. These costs include rent, utilities, maintenance, depreciation of equipment, and other indirect costs. The cost of manufacturing overhead is typically allocated to each unit produced based on a predetermined rate.
What is the Difference Between the Manufacturing Costs and Production Costs?
While production costs reflect all of the expenses associated with a company conducting its business, manufacturing costs represent only the expenses necessary to make the product.
Thus, production costs include several of the fixed costs and variable costs of operating a business. Additionally, raw material and labor costs are also included in the production costs. In contrast, manufacturing costs fall into three broad categories - materials, labor, and overhead.
For example, in production costs, the salary of the company accountant or the accountant’s office supplies are included in addition to the salary and supplies of the foreman. In manufacturing costs, however, only the expense incurred for the salary and supplies of the foreman is included.
What is the formula for calculating manufacturing cost?
The formula for calculating manufacturing cost is as follows:
Manufacturing Cost = Direct Materials + Direct Labor + Manufacturing Overhead
While the total manufacturing cost formula is a relatively easy calculation to make, we need some statistics to gain a more practical understanding of the manufacturing cost allocation in aviation MRO companies. Let’s have some benchmarks:
Labor Costs
Labor costs can account for a significant portion of an aviation MRO company's expenses. The cost of labor can vary depending on the type of work performed and the level of experience of the technicians. According to the research on Salary.com, the average Aviation Maintenance Mechanic salary in the United States is $89,822 as of January 26, 2023, but the salary range typically falls between $78,248 and $101,249.
While labor costs are already a significant expense for aviation MRO companies, respondents to the Oliver Wyman 2022 MRO survey are anticipating even more significant inflation in the near future, particularly in North America where labor costs are expected to rise by at least 5%.
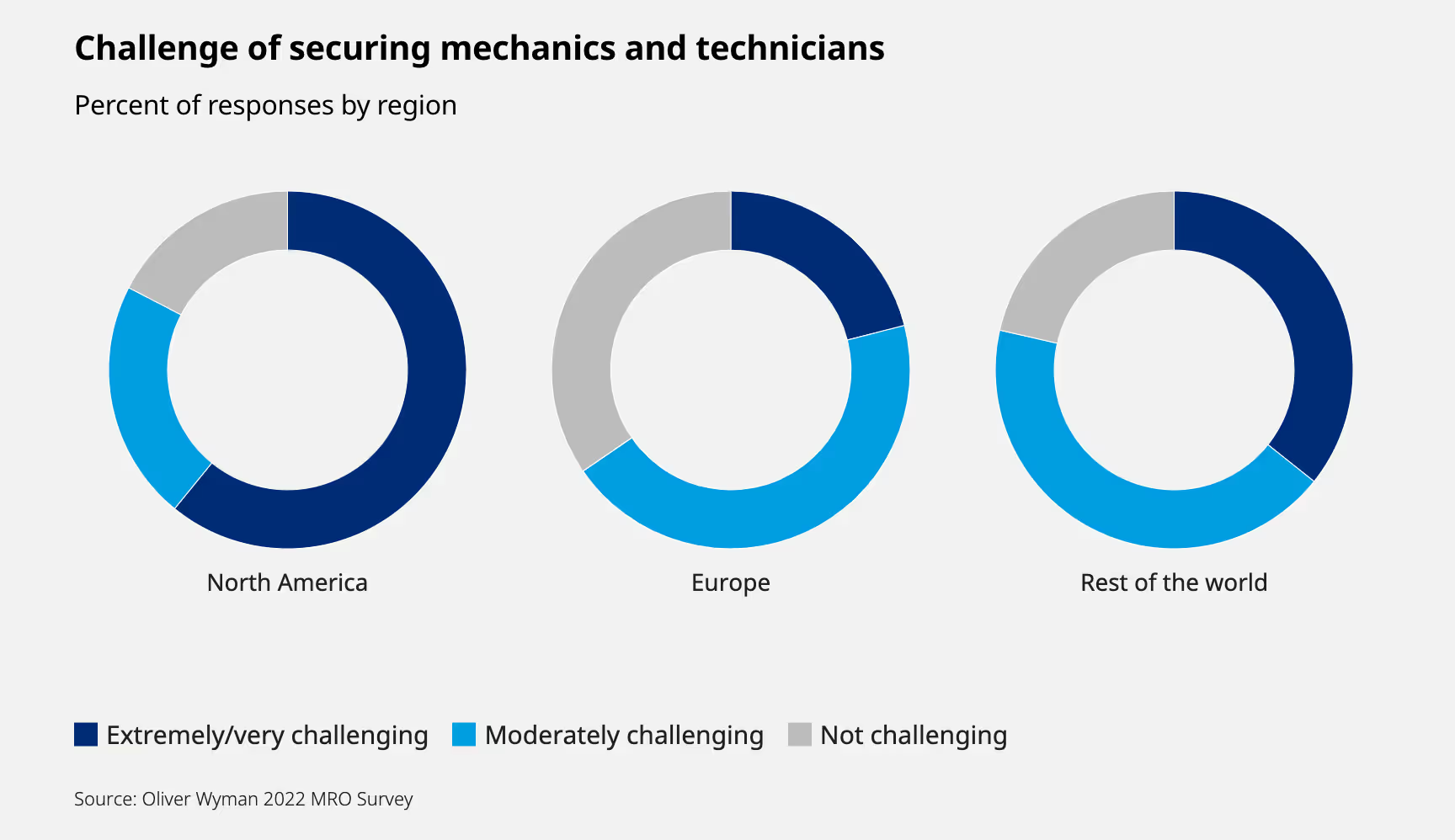
Material Costs
Material costs include the cost of parts, supplies, and other consumables used in the maintenance and repair of aircraft. According to Oliver Wyman's MRO Survey 2022, material costs accounted for approximately 30-40% of total maintenance costs for commercial airlines. Also, an average inflation of 5.5% for materials and 4.7% for labor is expected through 2023.
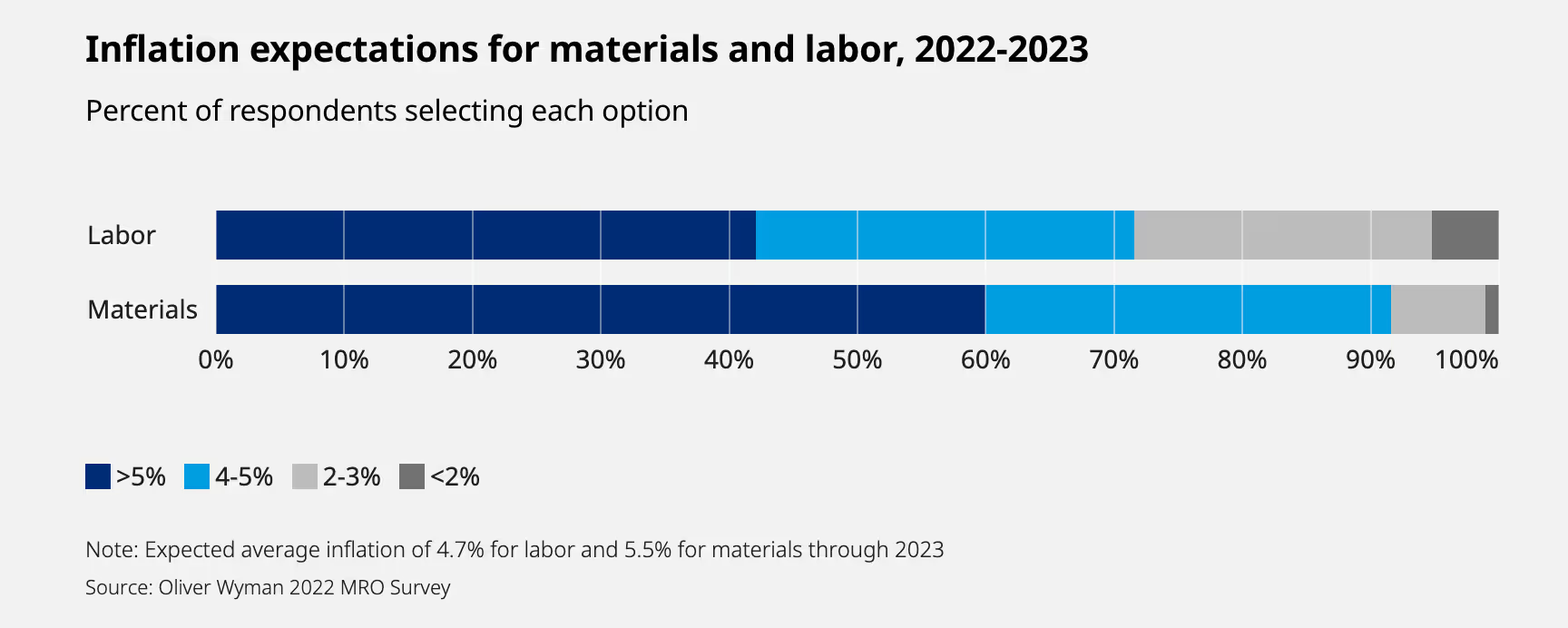
Overhead Costs
Overhead costs include all indirect costs that are not directly associated with the maintenance or repair of aircraft, such as rent, utilities, insurance, and administrative costs. According to the same Oliver Wyman MRO Survey, overhead costs accounted for approximately 20-30% of total maintenance costs for commercial airlines.
Cost per Flight Hour (CPFH)
CPFH is a metric used by aviation MRO companies to benchmark their costs against industry standards. It represents the total cost of maintenance and repair per hour of flight time. According to a report by Aviation Week Network, the average CPFH for narrowbody aircraft was $2,200-$2,400 in 2020, while for widebody aircraft, it was $4,200-$4,400.
Why understanding manufacturing cost is important?
Cost Management
Understanding manufacturing costs is essential to manage costs effectively. Knowing the cost of each product enables businesses to set appropriate prices and identify areas where costs can be reduced.
Profitability Analysis
Manufacturing costs are essential in determining the profitability of a product. By calculating the manufacturing cost and comparing it to the selling price, businesses can determine the profit margin of the product.
Decision Making
Manufacturing costs play a crucial role in decision-making processes. Businesses can use the manufacturing cost to determine whether to produce or purchase a product, whether to add a new product line, or whether to discontinue a product.
Budgeting
Manufacturing costs are an essential part of budgeting. Knowing the manufacturing cost of a product enables businesses to allocate resources effectively and set appropriate budget targets.
Product Costing
Understanding manufacturing costs is essential for product costing. Product costing is the process of determining the cost of producing a product. By understanding the manufacturing cost, businesses can accurately determine the cost of their products and set appropriate pricing strategies.
How Can Digital Manufacturing Improve Total Manufacturing Cost Management?
In today's fast-paced and competitive manufacturing environment, digital manufacturing has become an essential tool for improving total manufacturing cost management. Digital manufacturing involves the use of digital technologies such as computer-aided design (CAD), simulation software, and data analytics to optimize the manufacturing process.
Digital manufacturing can help businesses improve total manufacturing cost management in several ways:
Process Optimization
Digital manufacturing tools enable businesses to optimize the manufacturing process by simulating different scenarios and identifying the most efficient production methods. This optimization helps reduce the total manufacturing cost by minimizing waste, improving quality, and increasing productivity.
Predictive Maintenance
Digital manufacturing tools can help businesses predict maintenance requirements for their equipment. By analyzing data from the equipment, businesses can identify potential issues before they occur, reducing downtime and maintenance costs.
Supply Chain Optimization
Digital manufacturing tools can also help optimize the supply chain by improving inventory management and reducing lead times. This optimization can help reduce the total manufacturing cost by minimizing storage costs and improving efficiency.
Real-time Monitoring
Digital manufacturing tools enable businesses to monitor the manufacturing process in real-time, providing instant feedback and enabling them to make adjustments quickly. This real-time monitoring helps reduce waste and improve quality, ultimately reducing the total manufacturing cost.
Data Analytics
Digital manufacturing tools can also provide valuable data analytics that can help businesses identify trends, inefficiencies, and opportunities for improvement. By analyzing this data, businesses can make informed decisions that can lead to significant cost savings.
Conclusion
In conclusion, manufacturing cost refers to all the expenses incurred in the production of goods. The three main types of manufacturing costs are direct materials, direct labor, and manufacturing overhead. Understanding manufacturing cost is crucial for a successful business, as it helps a manufacturer determine the selling price of a finished product, identify areas where costs can be reduced, and evaluate the profitability of a product. By analyzing and managing manufacturing cost, a manufacturer can ensure the profitability and success of their business. Also, digital manufacturing can significantly improve total manufacturing cost management by optimizing the manufacturing process, predicting maintenance requirements, optimizing the supply chain, providing real-time monitoring, and providing valuable data analytics. As digital manufacturing continues to evolve, it is likely to become an increasingly essential tool for businesses looking to improve their manufacturing cost management and remain competitive in the marketplace.