Case Study: Improving on-time delivery of luxury watches through enhanced factory operations management
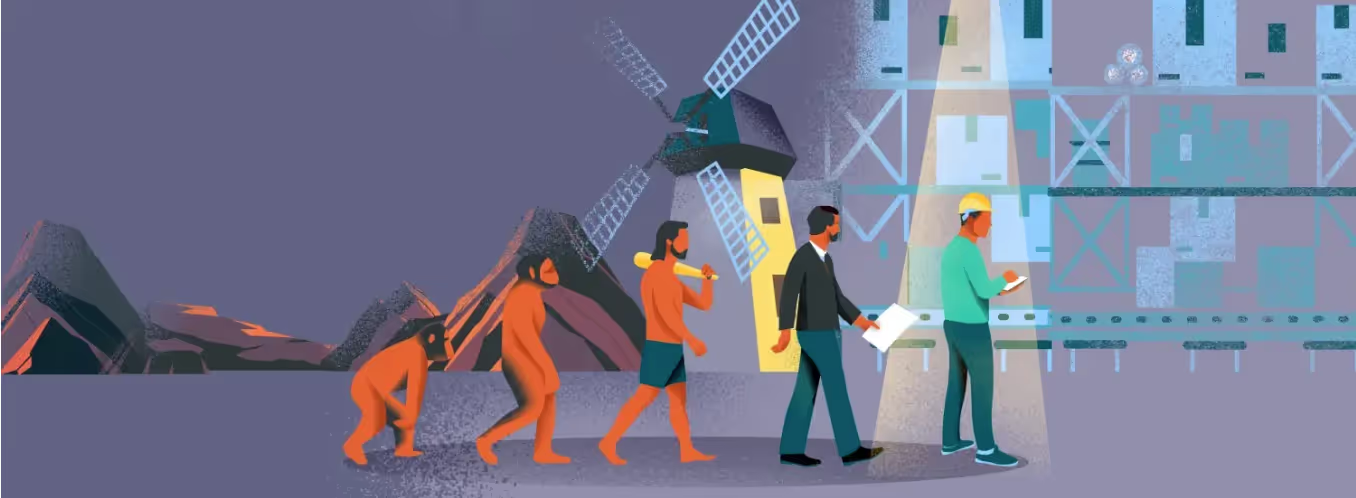
Due to the intricate design and hundreds of components needed for each watch, the production planning for watches is complex, and any disruptions in the supply chain can cause significant delays in production. This case study presents how a leading luxury watchmaker implemented Pelico to equip their factories with more agility and improve their operational performance.
Key factors causing supply chain disruptions
Luxury watchmakers depend on a highly complex supply chain. In the case of this market-leading luxury watchmaker, which produces over 2500 watches each day, each watch has between 100 and up to 400 components which are supplied by over 200 different suppliers. Needless to say, the potential for disruption is therefore extremely high. The company was searching for a solution that would enable operations teams to better anticipate disruptions while maintaining, or even increasing, production capacity.
The complexity in the watches production control and supply chain can be further dissected as follows:
- YoY growth: The market-leading luxury watchmaker experiences a 30% annual growth rate, placing significant pressure on production lines.
- Activity volume: The workshops produce approximately 2000 watches per day, including up to 400 components for each and over 200 SKUs.
- Number of suppliers: Over 200 active suppliers are involved in the production of the watches, increasing the potential for disruption in the supply chain.
- Factory workforce: The factory employs between 100 to 150 individuals to ensure the efficient production of the watches.
- Training time: Due to the complexity of the luxury watch industry, a significant amount of time and effort is required to train individuals to perform the necessary tasks.
Impacts on the supply chain performance and whole business
With such complexity in the factory operations, volatility can be sourced from various factors such as supplier delays, quality problems and missing parts, leading to decreasing performance and efficiency in the production, supply chain and whole business.
- Disrupted production schedule: Delivery delays create unplanned production blockers, which impact the delivery schedule for finished products. The same goes for delays in shipping or customs clearance. Both these types of bottlenecks put operations teams under immense stress, forcing them to chase after the facts.
- Decreased customer satisfaction: Luxury watchmakers have a global customer base, meaning delivery delays can have a significant impact on customer satisfaction and brand reputation. Customers may become frustrated if they have to wait longer than expected to receive their watch, and this can impact their perception of the brand.
- Increased costs: Additionally, unplanned production blockers increase costs. Firstly, inventories (as they can't launch some productions because of a missing part, components pile up in the inventory) and increased work in progress (as some missing parts are preventing some products from being finalized, they get stuck in the process). (both are a cost because they represent piles of money stuck in the process).
The implemented solution
This luxury watchmaker was looking for a digital solution that would enable its teams to work more efficiently and collaboratively in accordance with the production schedule.
Specifically, the solution needed to:
- Improve planning adherence: Pilot operations with greater precision and ensure that necessary supplies are available for work orders
- Digitize collaboration: Centralize and harmonize information to strengthen visibility
- Strengthen agility: Identify risks by alert monitoring and anticipating disruptions
- Facilitate decision making: Realize simulations quickly and share them
- Increase Efficiency: Remove non-value non-value added tasks
The watchmaker ended up adopting Pelico, a new AI-driven factory operations management system containing a 4-step solution to address each of these points.
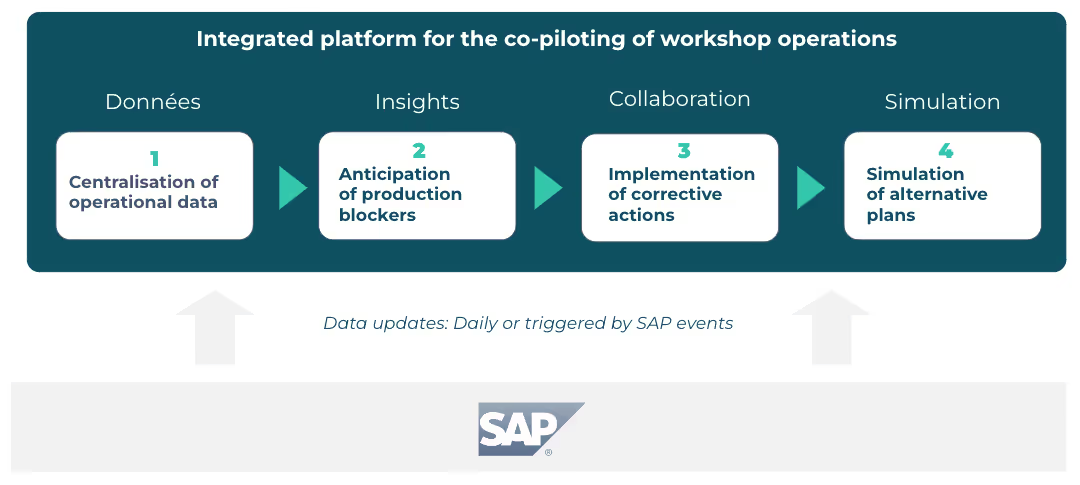
Step 1: Centralization of operational data
Centralizing operational data into one clear and comprehensive overview provided operations managers with real-time insights, enabled better planning, improved communication, and reduced downtime.
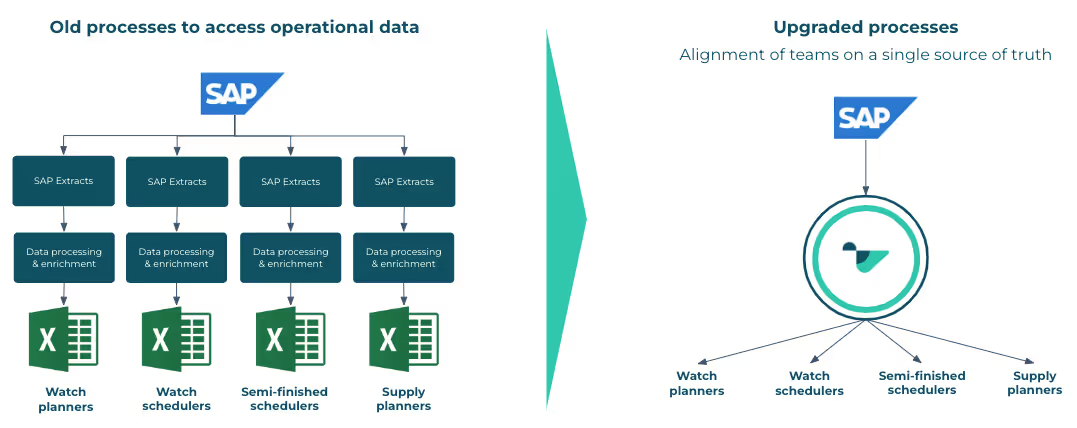
Step 2: Anticipation of production blockers
After gaining this new insight into key production metrics in stage one, and monitoring them closely, operations managers were then able to better identify production blockers in advance.
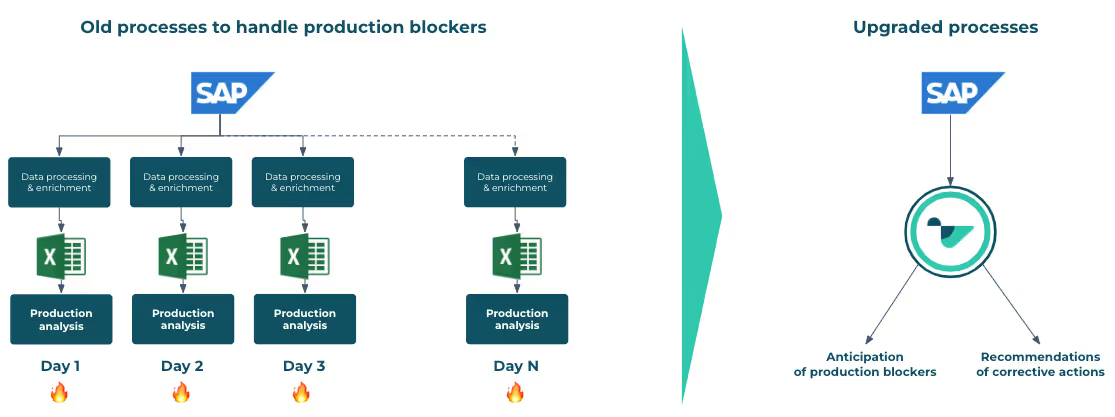
Step 3: Implementation of corrective actions
As a result, operations managers were able to take more, and better, proactive measures to prevent these production blockers from causing delays or disruptions to their production schedule — helping them adhere to planning schedules and secure high levels of output.
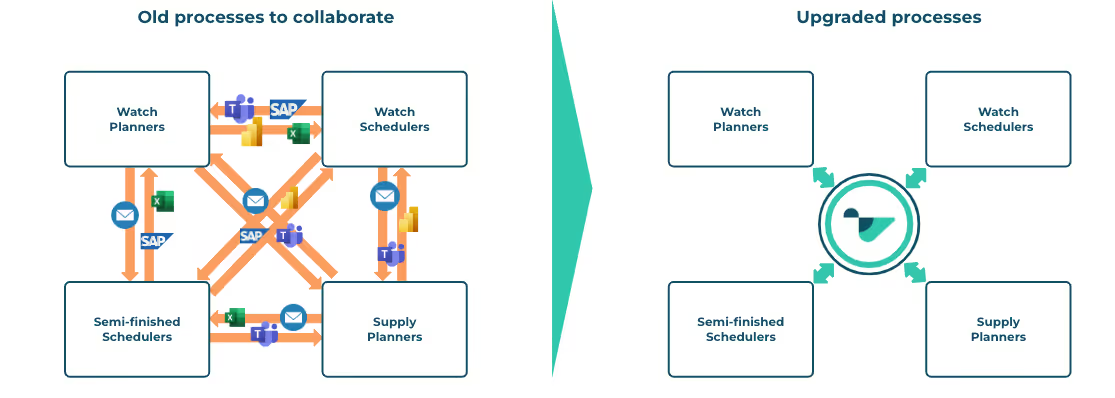
Step 4: Simulation of alternative plans
Last but not least, the solution enabled operations managers to go one step further and simulate many alternative plans, comparing and contrasting them to each other and choosing the most optimal route.
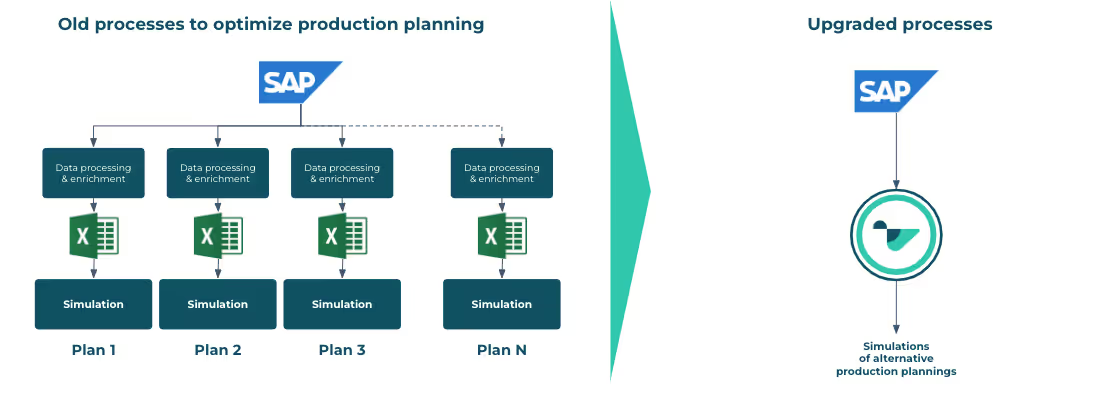
The business impact
Within a few weeks, this approach started to deliver tangible results.
- The watchmaker’s workshops increased their production capacity by 5% as a result of fewer bottlenecks due to the ability of operations managers to implement corrective actions more effectively, thus minimizing bottlenecks.
- At the same time, team productivity shot up by as much as 25% as time normally spent on gathering data and making sense of the facts could now be used on value-added activities such as corrective actions.
- The main objective of the solution was achieved: adherence to the planning schedule went up from 69% to 95% — a nearly perfect score.