How Operational intelligence helps anticipate production blockers for an aerospace plant
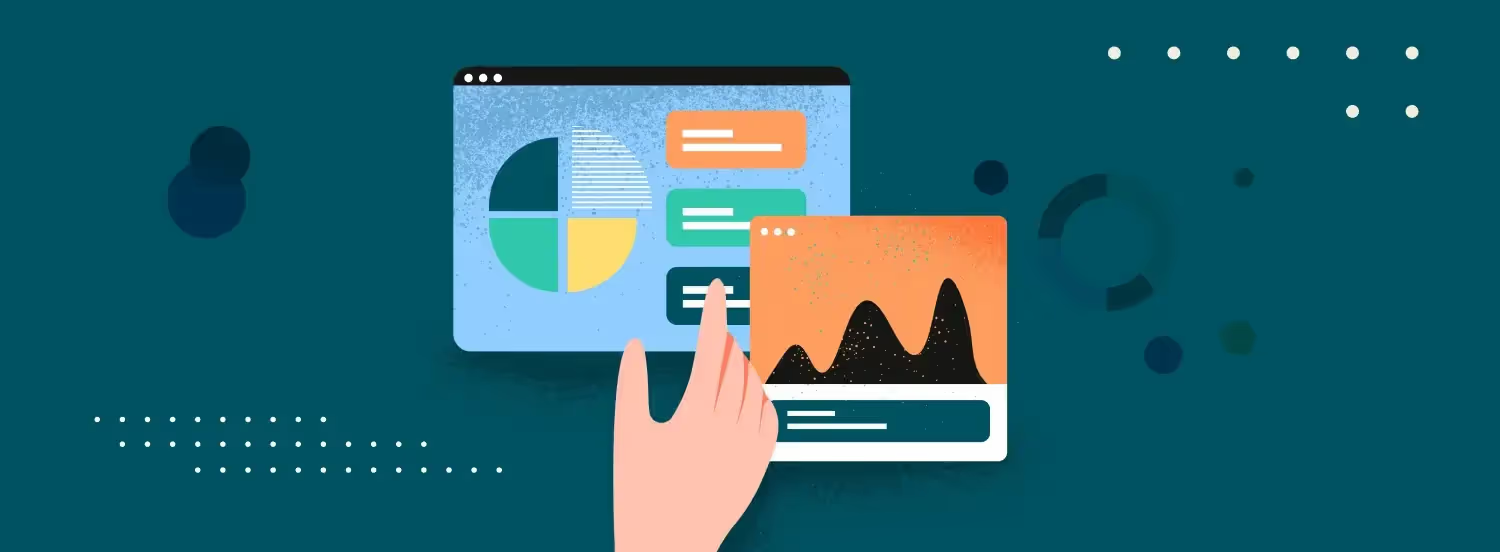
The background: time-hungry plant seeks digital booster
The plant we’re writing about specializes in the production, integration and maintenance of flight actuators. Just like the rest of the industry, the company was hard-hit by the COVID-19-related crisis. Sharp drop in business volume has entailed spending and staffing cuts, with a headcount reduction of about 10%. Hence the need to do more with less.
How? By leveraging the benefits of digital technology. The plant started implementing Operational Intelligence solution Pelico in the spring 2020 with a view to improving productivity and efficiency.
Digital transformation had become a matter of survival as we needed to do more with less. Production Control Manager, Aerospace.
Challenges & requirements
Making crucially needed information available to all
Everyone across the plant needs visibility into the Master Production Schedule that consolidates all production-related data. For example, production managers need information about upcoming production orders, resource availability and inventory levels in order to figure out whether capacity and stocks match inbound demand. Production controllers need to be aware of the delays that may jeopardize on-time delivery, so that they can focus effort and resources on the deliverables that are threatening to slip into the red zone. Then, finding mitigation plans requires data about the lead times of operations in order to reschedule activities, or about labor costs in order to decide whether to hire temps or schedule employee overtime.
But, before Pelico, all that production, staffing, supplier and inventory data used to be stored in the plant’s ERP — a complex piece of software that most workers can’t handle for lack of technical background and savvy. A handful of key people with the required IT skills were needed to extract the data and convert it into Excel-based tables and graphs.
For example, whenever someone needed to know whether the inbound part shipments would enable the facility to execute on the production plan, a Production Controller or one of the other logistics team members had to comb the ERP to find the right supplier transactions, then format the data in Excel to provide actionable information: which supplier would deliver which parts, how many, and when.
Such time-sensitive questions have to be answered rapidly lest missing parts block the production. But data searching and reporting used to tie up Production Control teams for hours and days, which delayed response. What more, that time was diverted from productive activities. In other words, it was wasted.
Increasing data agility
Once the data was extracted and formatted, the insight was as if set in stone.
It is impossible to extract all the information from the ERP. So we’d pull out data and generate Excel graphs based on specific queries. For example, we’d perform an extract to show the number of parts placed in stock over the previous week to help operational teams assess availability. But then, the next day, a manager would step in and ask for a monthly or quarterly view of stock value to evaluate inventory holding costs, and that’d take a whole new extract, the Production Control Manager explains.
“Also, the year 2020 has introduced new points of attention for production managers. When assessing supplier delivery risk, we’ve had to take into account the sanitary restrictions in force locally. We needed increased ability to play with the data”.
Enabling effective collaboration
Cross-team collaboration is at the crux of industrial operations. A case in point is the supply chain: production teams need to be updated whenever potential or actual supplier delay puts the production plan at risk. They need reliable revised ETAs from Sourcing & Procurement teams in order to adjust the plans accordingly and make sure production isn’t blocked. Conversely, the Supply teams need real-time updates on operation schedules in order to determine whether supplier delivery will meet production requirements.
Among the limitations of spreadsheet technologies are poor collaborative capabilities. For lack of dedicated collaboration tools, most of the information was circulated through emails. In addition to the frustration that comes with a full, constantly pinging inbox, in addition to the difficulty of retrieving specific data from lengthy email threads, this meant that the information was only shared between specific senders and receivers.
Whenever someone was away on leave, the colleague who took over had no way to access that kind of in-mail information — other than hunt for it.
With hard-to-get data, rigid extracts, and silos hindering information sharing, teams were spending about half their time searching or waiting for the information needed in order for production to proceed. And the downtime was weighing heavily on overall productivity.
Pelico acts as an intelligent layer that sits on top of transactional systems and reconstitutes a digital twin for operations. A collaborative and intelligent platform provides AI-driven insights for smart prioritization and problem mitigation The goal? To empower operational teams to cut through the fog of uncertain operations and achieve predictable outputs. Learn more.
The benefits of Pelico
Everyone gets the right information at the push of a button
With Pelico, support teams, managers and operators can instantly and easily access the data they need, regardless of their technology maturity or background. Where the data used to be locked in a hard-to-navigate system, it is now readily available in a user-friendly interface with production-oriented apps.
Looking for specific data? Just apply a few filters, and here it is. You can customize the time frame and scope, drill down at granular levels and select the kind of formatting that you want.
As a result, understanding what is required in order for production activities to deliver on customer commitments — for instance assessing a delay in production and its impact — now takes 3 minutes where it used to require 2 days. “Pelico empowers us to respond much faster to operational issues or questions — for example, How long until production is blocked? Which part is the most crucially needed and should be delivered at all costs? What’s the delay in production at the plant level?”.
Data intelligence and insight enabling production control
As Pelico extracts the required information from the ERP to duplicate it onto a distinct information layer, it becomes possible to play with the data without tampering with the transactional connectors that link the plant’s records to those of suppliers or clients, and without compromising the integrity of the master data. This opens up the opportunity to run what-if simulations. Want to assess the impact of a delay in a supplier delivery on the production schedule? Just run a scenario.
That kind of data intelligence and predictability is invaluable to Production Control teams, which are in charge of planning operations and ensuring proper completion of production activities. They are responsible for making sure that the right parts are available as planned, that the resources with the right skills are available at the right time and optimally allocated, that the tools and equipment are in working order… Long story short, they coordinate countless variables. “Our job really is about managing uncertainty and risk. We need the ability to anticipate any blocker and make sure that everything is fixed by the time operators start working”. By cutting through the fog of uncertainty, the Operational Intelligence solution supports increased responsiveness and improved ability to deal with unexpected problems and overcome obstacles.
The Production Control Manager particularly appreciates Pelico’s capabilities for detecting risk and missing parts. “Based on production orders and stock availability, the platform lets me know which part will be needed, and when is the next planned delivery — all in a few clicks. Getting this kind of key insight used to require a lot of tedious manipulations”, he says.
Seamless collaborative experience
As Pelico breaks down information silos between Customer, Supply Chain and Production teams, the time needed to share information and solve problems is drastically reduced. Pelico’s platform includes an escalation engine that supports collaborative problem-solving: when a team member is not empowered to make a call and solve a specific problem, they can just escalate it by assigning a task to the right person, at the push of a button.
The collaborative platform also offers the ability to send out notifications, comment on work items and get instant response. Everyone can see the comment history and get up to speed in minutes. A team member is wondering about part availability or production deadlines? Most of the time they’ll be able to find the answer by themselves on the platform. When not, it is now as easy as pie to reach out to the right person and get a prompt response.
Facilitated communication and collaboration also accelerates and improves collective decision-making. Even when working remotely, teams can work together more effectively and efficiently.
Finally, “Pelico brings to the plant the fast navigation and great look and feel that we’ve grown so accustomed to in our daily lives. Better experience helps us become more agile. That’s a productivity driver too.”