Why Business Intelligence (BI) tools aren’t useful for front-line workers?
%202.avif)
Growth and widespread adoption
There’s no doubt about it: the popularity of business intelligence, a.k.a. technology that helps businesses make sense of their vast amounts of data, is on the rise across all industries. A recent report by Grandview Research predicts a steady 10% compound annual growth rate for the business intelligence software market in North America in the next five years.
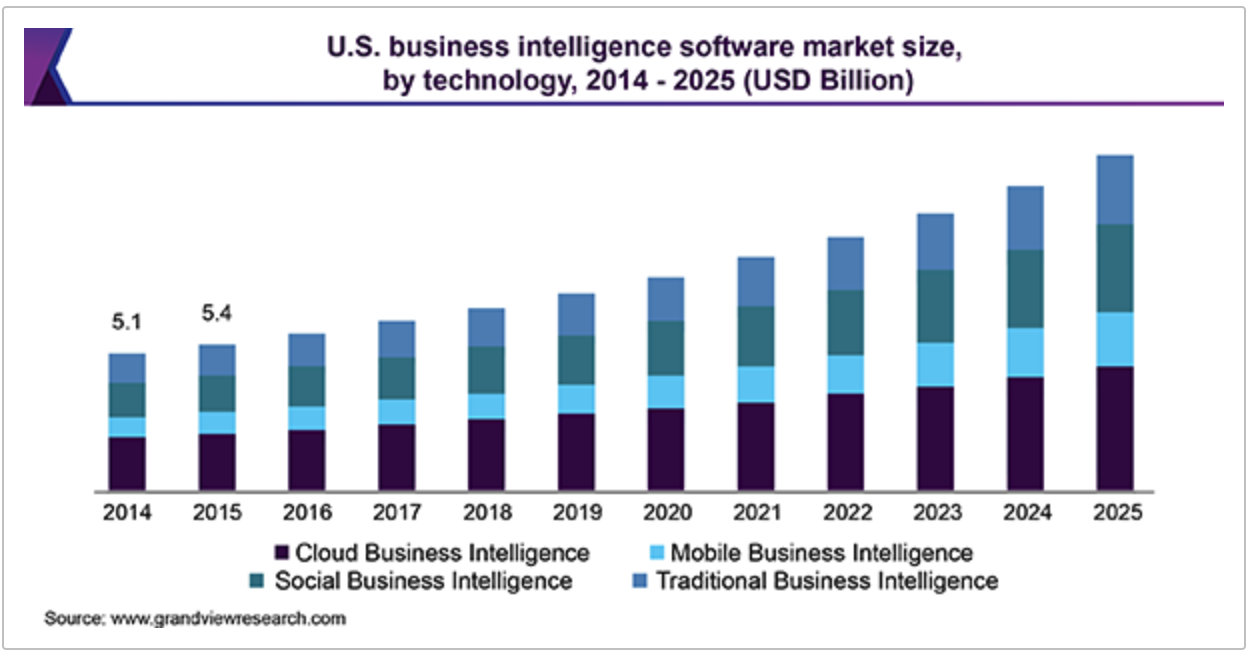
It is no surprise, then, that BI has also started to be adopted in the manufacturing industry, where managers are increasingly relying on BI for their decision-making process. And that’s not for nothing: from more efficient reporting and more accurate figures, to better performance monitoring, these analytics provide managers with vital insights into manufacturing processes.
Yet, when it comes to operational teams in the manufacturing industry, BI doesn’t provide the contextual analysis that operational teams need to solve problems and make good decisions. But before getting into the reasons why, let’s elaborate some more on what BI is good at.
The power of business intelligence tools
Above all, BI tools provide useful ways of visualizing data, making it easier to draw actionable results. Here are the key advantages to manufacturing managers provided by BI tools:
- Real-time analysis of bottlenecks through advanced flexible dashboards
- Machine/cell performance (uptime, downtime, reasons for both)
- Scrap rates, production performance, quality (actuals)
- Throughput (scheduling, production vs. actuals)
- Real-time analysis of bottlenecks and shift performance
- Ability to slice & dice the data into different types of charts
- Ability to join different datasets in order to produce reports, and better performance monitoring
If this sounds vague, let’s take a specific example. In manufacturing, old school spreadsheets have long reigned supreme. But spreadsheets don’t allow you to see data in real-time. Take unplanned machine downtime, for instance. A manager using a traditional spreadsheet has no way of knowing about the issue until after it’s happened.
Putting out future fires
So far, so good. But why is BI not suited to operational teams? Simply stated, BI isn’t very good at helping operational teams figure out where the next fire will come from. BI dashboards are like rearview mirrors: they help us understand past performance, but don’t offer good visibility on the road ahead.
Imagine you’re a supply chain worker. A BI dashboard is capable of informing you that there are a total of 17 missing parts. But what you really want is answers to dozens of follow up questions. Where is the bottleneck taking place; in transport, at the supplier, or at the reception centre? Which essential steps in the production chain are being hampered by these missing parts? And, most importantly; what is the optimal way of rescheduling production to minimize the harm done by the delays?
While BI tools can provide real-time updates on the status of these missing parts, they do not help answer these crucial follow-up questions that lead to an optimal mitigation scenario. In the end, operational teams care about the future—about what bottlenecks will arrive tomorrow, and how to anticipate and mitigate them. BI technology has not eliminated the need to simulate new scenarios and put out future fires.
Operational Intelligence: what operational teams really need
Above all, operational teams want to understand where the next fire will come from and how to best put it out. They want to move from reactiveness to anticipation. And for that, Operational Intelligence—not Business Intelligence—is the most useful approach.
What does OI look like in practice? In layman’s terms, we’re talking about a user-friendly interface requiring little data savviness to operate, which enables teams to prioritize their work according to the most impactful actions by providing a prioritized list of alerts along with their associated consequences. This interface also offers instant access to contextual data, enabling a workflow which displays problems down to the granular level, complete with actionable recommendations.
The operations research algorithms powering such interfaces are often more effective than humans at reallocating resources and rescheduling orders for optimal sales funnels or on-time-deliveries. They also enable operational managers to simulate alternative scenarios by changing the input variables ("if I do A, how does that affect B and C, etc.?”).
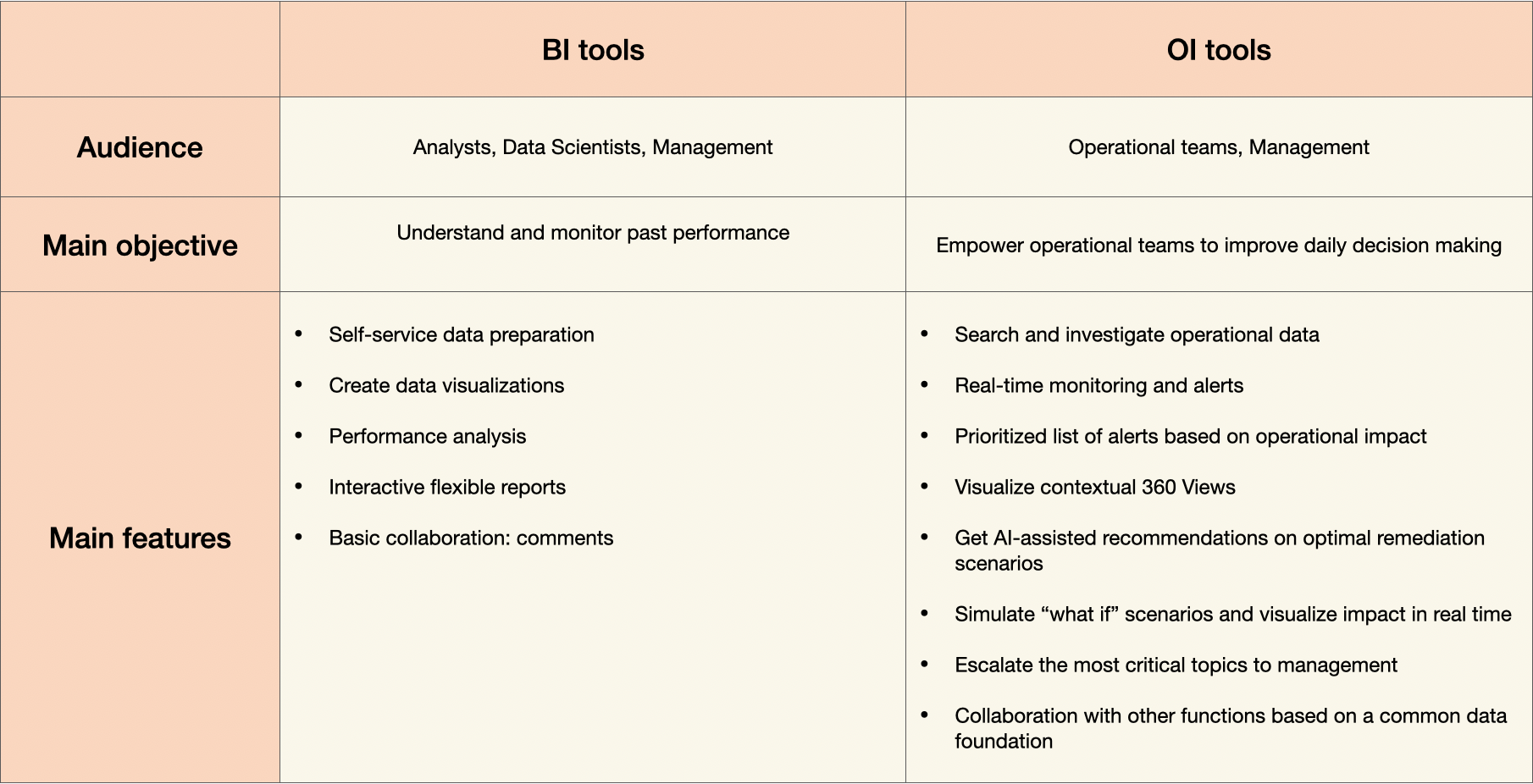
From retroactive to proactive operations
After transitioning to the digital world by increasingly relying on BI tools to track performance, manufacturers are now perfectly poised for the next evolution: unlocking the potential of OI. Where BI helped teams understand their past performance, the tech underpinning OI is now mature enough to equip operational teams with a compass that can help them steer in the right direction ahead. These digital companions will become a vital component of operational teams in the future, and there are more and more companies like Pelico which offer solutions designed specifically for operational teams to help them achieve predictable outputs, enabling fires to be put out before they even happen!