How modern tools can help factory managers manage bottlenecks
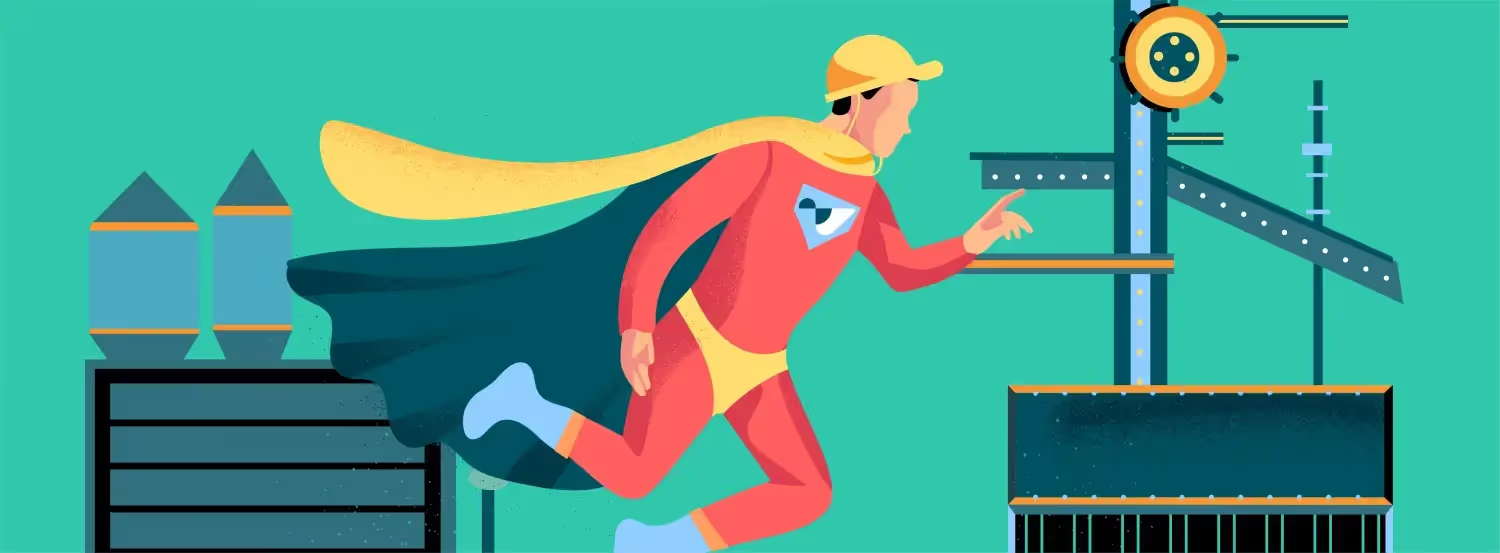
Times are rapidly changing for factory managers—and not just because of the disruption of global production and supply chains caused by the Covid-19 pandemic. With shortened production cycles and an explosion of unknown variables, factory managers are struggling to run their operations smoothly. From late deliveries, to machine breakdowns and customer demand varying by the hour, agility has become the name of the game.
Yet, in 2021, the overwhelming majority of factory managers are still reacting, instead of anticipating, to changes in manufacturing operations. That’s because they lack critical oversight—one place that centralises all the data they need to make better decisions.
Why bottlenecks are bad
First, let’s give credit where credit is due: managing industrial operations has always been a complex problem. In assembly plants, managing bottlenecks was often a matter of managing people (by appropriate staffing and task leveling) while in process plants, equipment capability tended to be the disrupting factor. And in both cases, supply chain forecasting has always been an issue for factory managers.
But, in today’s data-driven globalised economy, complexity isn’t just a byproduct of industrial manufacturing—it’s the beating heart of it. Managers and teams need to constantly think on their feet and react to an overwhelming amount of variables that interact with each other in complex ways.
This inevitably leads to blind spots, asymmetric information and suboptimal decisions that end up bottlenecking your operations. And that, in turn, has several major consequences.
- It’s bad for business. In terms of cost, bottlenecks are estimated to put a $12 trillion dent on the global production market. It is estimated that factories that do manage to leverage data in daily operations can increase their profitability as much as 30% by rendering processes more efficient. Another factor is savings: digital enablement can result in as much as $800k in savings per month across the board from increased productivity, safety, and agility.
- It’s bad for managers: It is estimated that factory managers and teams can spend up to two thirds of their time each day simply gathering information. This cumbersome task often leads to stress and confusion, not to mention internal communication issues which cause even more delays.
- It's bad for customers: In the end, bottlenecks in the production cycle end up affecting the client more than anyone else. When projects get delayed, they go over budget from the added cost of delays, leading to a nearly 40% waste of industrial output even before it reaches your customers.
The power of intelligent operations assistance
But technology can offer a way out of this mess. In recent years, progress in Data and AI have enabled the creation of platforms which centralize huge amounts of data and provide factory managers with the critical oversight they need.
Imagine showing up in the morning and logging in to a user-friendly interface—a dashboard of sorts—where all aspects of your operations are visible. The different teams—Production, Quality, Customer support—can consult this information to align over common goals and get shared visibility on bottlenecks. Imagine a system where front-line workers are empowered with personalized recommendations on how to solve certain key issues, or react optimally to daily volatility by for instance consulting computer-generated production plannings.
These are just some examples of what data-driven operations management can do to make things run smoother. Rather than automate or take away certain responsibilities from factory managers and teams, these platforms help overcome information silos. They offer intelligent assistance for operational teams, which helps them make better decisions.