Disruptions in Supply Chain: How to Manage and Avoid
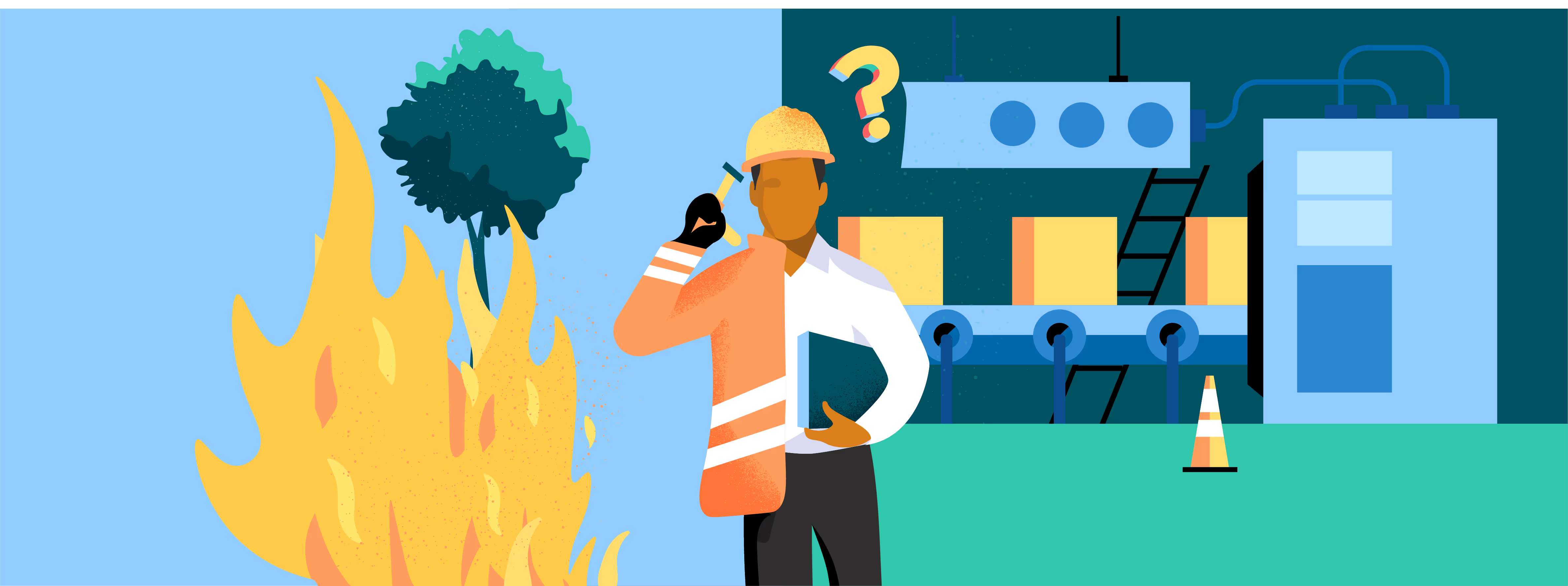
The past three years have added a new meaning to disruptions in supply chain. While supply chains are constantly shifting to respond to fluctuations resulting from social and geopolitical events, no one could have predicted the impact of Brexit, the Covid-19 pandemic and the war in Ukraine—to name just three examples—on manufacturing in 2023.
Situations change much faster than teams can reliably plan for. Every time that manufacturers pivot their strategy to adapt to a global event, production and operations planning are significantly affected. Put simply, the manufacturing industry is not currently equipped to deal with the disruptions in supply chain of a rapidly fluctuating world. Whereas previously ERP systems were capable of providing sufficient visibility to handle the day to day, the exponential speed at which the industry is evolving forced many managers to switch to more flexible tools such as Excel spreadsheets and messy email chains. But this is a temporary and highly suboptimal fix, as these tools just aren’t able to handle issues as efficiently as needed. They are also creating stressful conditions for operational teams who are constantly fire fighting and chasing after data.
In short, faced with so many unexpected disruption in supply chain, it has become imperative to build a culture of resilience within manufacturing firms. This involves shifting to an agile approach that affords factories and supply chain teams greater autonomy to deal with fast-moving challenges as they arise.
What can cause disruptions in supply chain?
Internal or external factors might be the source of disruptions in supply chain in several businesses. The following are the typical factors that may create these interruptions:
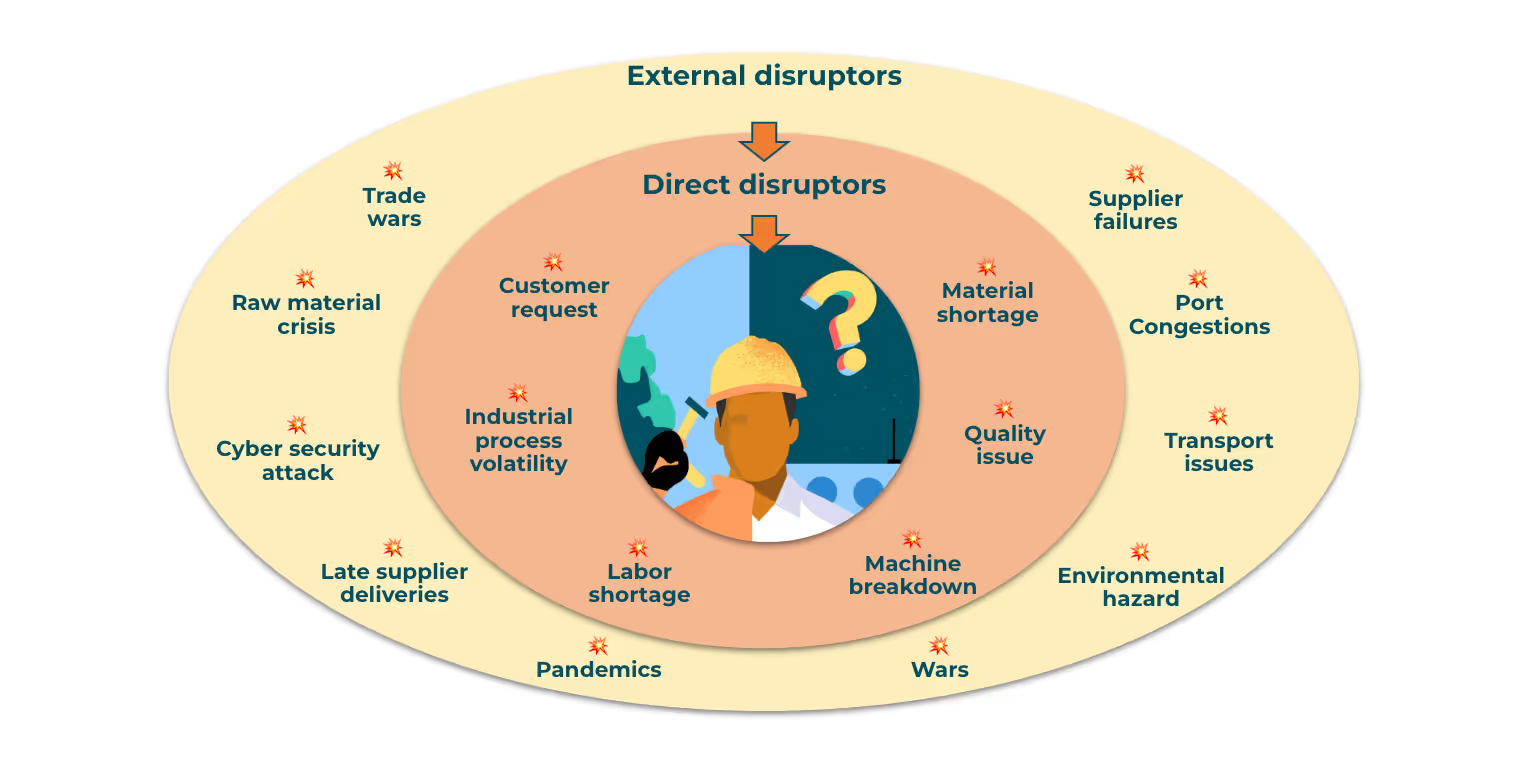
Pandemics & Natural Disasters
In the previous year, we’ve seen how the Covid-19 epidemic wreaked havoc on global supply chains across sectors. The magnitude and effect of global pandemics and public health emergencies may be devastating to supply networks. It has an impact on SCs, the individuals engaged, regions, and multinational organizations at every level of the manufacturing process.
In 2011, an earthquake off Japan’s Pacific coast triggered a tsunami, resulting in a nuclear accident at the Fukushima Daiichi Nuclear Power Plant. This nuclear disaster had an impact on all small enterprises and the worldwide economy since it halted manufacture of the world’s supply of 300-millimeter silicon wafers (a key component used in semiconductors) and other following critical parts. Tsunamis, hurricanes, wildfires, and floods expose supply chain flaws in the broader SC structure.
Logistics Delays and Failures
Globalization and increased commerce have made overseas providers more frequent in supply chains. As a result, there are more economic prospects, but there is also more demand on international and local transportation networks, resulting in congestion and delays.
Supply networks can intensify logistical issues by introducing unknown factors. A catastrophic event can disrupt the delivery of goods and services in an affected region, or a country can enter lockdown, thereby making it impossible for carriers to transport commodities by land, air, or sea, even in the case of a pandemic.
Price Fluctuations
Price changes for suppliers in your supply chain can also trigger changes since you must decide whether to switch suppliers, raise your own rates, or see your profits lowered by covering the expenses yourself.
Price changes can be prompted by a wide range of factors. Commodity prices, for example, like crude oil are generally unpredictable and can have a significant effect on the financial overhead of a variety of transportation and manufacturing elements.
Failure in quality assurance and management
Quality assurance and management are critical components of supply chain management. A problem with the product can develop at any point in the supply chain, causing the company to miss the deadline for releasing the final product. Businesses do not want to offer poor quality goods or delay shipments because of faulty products. Providing a strong quality assurance across the supply chain is imperative.
What is the impact of disruptions in supply chain?
Ongoing disruptions in supply chain have impacted manufacturing firms across the world in a variety of ways, including:
Increased supply costs
As if disruptions in supply chain aren’t enough, the increased demand and growing inflation concerns are leading to higher material and supply costs. If your organization, like many, is already facing budget constraints as you try to navigate in a post-pandemic market, higher supply costs make this process even more difficult. Now, companies not only have to develop new supply chain networks that allow them to secure the raw materials they need, but they must also make cost efficiency a top priority.
On top of this, businesses are facing yet another uphill battle — increased fuel costs. The Russian-Ukraine conflict has driven fuel prices higher on a near-daily basis. In the United States, gas prices have hit an all-time high and petrol costs in Europe have spiked as high as 62% in some areas.
These increased costs, in turn, are being passed on to organizations that are already dealing with higher costs due to demand and inflation. Companies must make tough decisions regarding their supply chain network to control costs if they hope to remain competitive.
Inability to meet customer demand
According to a recent study, organizations’ biggest supply chain challenge is securing raw materials from suppliers. Some of these business leaders admit that lack of diversification in their supply chain network is partially to blame, but also note that suppliers’ inability to keep up with technological advancements is also hindering supply chain processes.
No matter what the reasons are, if your company can’t secure the materials it needs for production, it can be next to impossible to meet consumer demands. We can see this failure in the supply chain process by the number of empty shelves in stores around the globe.
For your business, however, this failure in supply chain distribution means more than slow delivery of products. It could cause the loss of customers, diminish revenue and ultimately affect the future success of the company. It’s crucial to take steps to strengthen your supply chain networks and processes to improve efficiencies and meet consumer demands.
Longer lead times
Even if your company is able to secure the raw materials it needs for production, the combination of delivery delays and talent shortages can lead to longer lead times or the time it takes to complete an order. As a business leader, you already know that any delay in the production process is costly. It can decrease production, diminish customer confidence, reduce sales and impact revenue.
Typically, companies have the capabilities to mitigate a few disruptions within the supply chain. The current supply chain shortages, however, are impacting everything from production to delivery. It’s causing a bottleneck in production processes across industries. For example, the computer chip shortage led to an 11.3 million production unit loss in the automobile industry alone. Another example impacting the auto industry is the shortage of wire harnesses due to the Ukraine-Russian conflict. Car manufacturers, including BMW, Volkswagen and Porsche, have already announced production disruptions that are likely to last months until alternative suppliers are found.
As all business leaders know, longer lead times can result in lower output, higher costs and reduced revenue.
How to manage and avoid disruptions in supply chain?
Disruptions in supply chain can only be effectively identified and prevented once we are able to monitor, in real-time, the planning feasibility. This means instead of continuing today’s approach of systematic management, operations managers need to move towards exceptions-driven management. In other words, they need to use data insights to help them better prioritize the production plan.
Anticipate production blockers at granular level with better insight into data
Being several steps ahead of the game allows operations managers to have better foresight and gives them greater agility to respond to disruptions. Many, if not all, disruptions in supply chain can be anticipated ahead of time with the help of advanced analytics, such as lengthy quality inspections, expired supplier contracts, lower yield than expected, late internal production operations and so on.
It goes without saying that the sooner disruptions in supply chain are identified, the easier it is to deal with them. Take, for instance, the case of a missing part; AI can automatically suggest the "next enablement" date to reschedule a given work order and alternative work orders to carry out in order to avoid losing capacity. However, in the current set up, operations managers are all too often forced to dive into various siloed systems and processes involving different teams before being able to work towards a solution.
Receiving, and acting on, quick recommendations
Another essential strategy for operations managers to manage disruptions in supply chain is obtaining swift recommendations that enable supply chain & production control teams to make informed decisions. This strategy can be applied in the following areas:
Managing purchase orders
Advanced analytics can help operations managers in factories synchronize their supply chain orders with their real production needs — all in real-time. This means they are able to plan their purchase orders more effectively by analyzing data from various sources, such as sales forecasts, production schedules, and inventory levels, and prioritize parts based on real production signals (e.g. stock below target stock security level, over lead time) rather than "noise", thereby gaining visibility into what will block the production line and jeopardize sales.
Suggesting stock transfers
Advanced analytics can also help predict demand patterns and optimize inventory levels to minimize stockouts and reduce excess inventory. More importantly, they can offer highly valuable signals to operations managers on when to transfer stock in the most efficient manner to minimize disruptions and maximize output.
Identifying blocked stock
By analyzing data from various sources, such as quality control reports and production data, advanced analytics can help operations managers identify disruptions in supply chain. Algorithms trained on anomaly detection and clustering can identify issues with quality control, thus helping operations managers take proactive — rather than reactive — steps to improve the health of their inspection queues.
Improve your production plan
The third strategy that operations managers can apply is to define their operational goals and constraints before optimizing their production planning. As new constraints or bottlenecks appear due to daily volatility, teams should be empowered with the agility to react in an optimal way in coherence with the operational strategy.
Just as Waze or Google Maps automatically reroutes users when there is a traffic issue, advanced analytics can help operations managers monitor the projected on-time delivery of parts and take decisions based on a huge quantity of variables.
Optimize part allocations & better calculate tradeoffs
Imagine a situation where an order is being blocked by one missing component — and this occurs after another order was blocked by the same component, and so forth. The best course of action is to change the order, knowing that there will be a refill. This can only be done with the help of advanced analytics.
Similarly, when a part becomes scarce and is necessary to manufacture different products, data can help prioritize the product to manufacture in priority and assess the impact on other products. advanced analytics are also extremely effective at analyzing service records and customer data to identify opportunities to use used parts in service orders. Not only does this increase profit margins, but by looking at a wider sample of options, advanced analytics can help identify a greater number of available parts. This has the added benefit of increasing the life expectancy of equipment based on serviceable hours potential.
For example, in the aviation industry, a part with 1000 hours of flight potential can only be allocated to equipment with less than 1000 hours of flight time to avoid reducing its lifespan. These recommendations are made algorithmically, thus eliminating the potential for human error.
Increase reliability of customer delivery dates
By breaking the wall between commercial & operational teams, advanced analytics can help synchronize customer demand with production plannings. That means teams can know in real time if demand is covered by the production planning and identify gaps at granular level, as well as anticipate delivery blockers in advance such as material coverage, late production, administrative blockers (such as export control certificates), quality control blockers, financial blockers, and even transport availability. Once these have been identified, operations managers can formulate mitigation scenarios for each blocker, for instance by rescheduling production, increasing quality control capacities, or expediting transport and delivery services.
In a nutshell, AI allows them to statistically estimate production end dates and delivery dates while taking into account all blockers and their resolutions. By accelerating the feedback loop with the customer, this generates greater customer satisfaction and better quality service.
Automatically estimate shipment dates
Enlisting the help of sophisticated algorithms such as Pelico’s, which analyze material coverage and capacity feasibility to come up with highly precise shipment estimates, operations managers can be much more certain about when essential parts will be delivered.
Conclusion
In conclusion, supply chains are under extreme pressure due to growing volatility and constant disruptions. However, supply chain managers currently do not have the right technological tools to adjust their schedules and get the visibility they need. ERPs are no longer fit for purpose, and messy email chains and Excel sheets are just temporary bandaids on a bigger wound.
The solution? Companies need to transfer more agility and autonomy to factories to turn them from oil tankers into speedboats. Tools combining data and collaboration unlock powerful possibilities to facilitate this transition because, among other things, it allows supply chain managers to centralize operational data and gain better visibility. From anticipating bottlenecks with algorithmic computation, to assessing planning feasibility and streamlining collaboration across teams — the combination of data and collaboration empowers factory teals to quickly implement the right decisions.