Why Waiting Could Set You Back: Act Now to Bring Resilience and Efficiency to Your MRO Operations
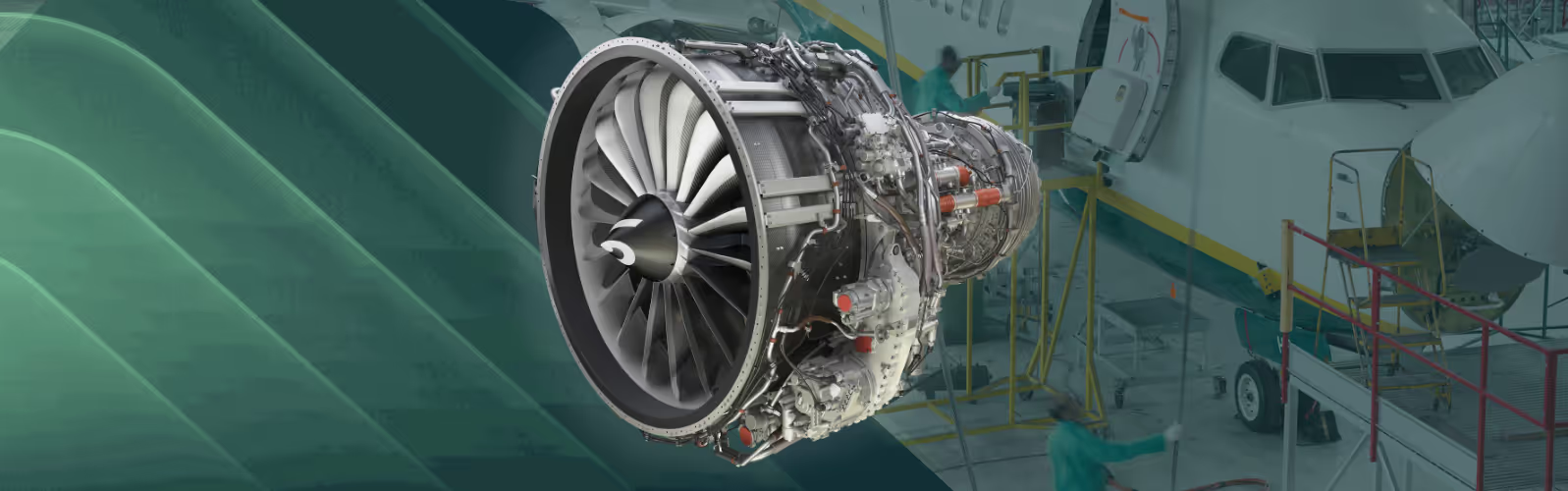
We are aware that aircraft engine MRO shops are currently experiencing a capacity shortage, turning them into a bottleneck for commercial aviation. To make matters worse, a study done by Bain&Company forecasts that the demand for aircraft engine maintenance and repair will peak in 2026.
Seeing that there was no offering in the market that empowered MRO managers with the agility and resilience needed to overcome this capacity crunch, we, at Pelico, have been on a mission: to build a bespoke solution that helps professionals efficiently manage complex MRO projects, such as the maintenance and repair of LEAP and Pratt&Whitney GTF engines.
However, before we go into the details of Pelico's MRO aircraft engine offering, we'd like to walk you through some of the insights we've uncovered and why we believe now is the right time to act.
Our analysis shows that aircraft engine MRO demand is likely to experience a near-term peak in 2026 and remain constrained through the end of the decade
Jim Harris, co-leader of Bain’s global Aerospace and Defense practice
An entirely new game: How COVID-19 redefined the engine maintenance industry
The COVID-19 pandemic has had a profound impact on many industries, and air travel is certainly one of the most affected. This is especially pronounced in one of the sector's biggest and most expensive segments: engines.
Plummeting passenger demand and deferred maintenance
With passenger demand at an all-time low, in addition to travel restrictions and economic recession, airlines were forced to cut costs. One of the ways they managed to do so was by deferring shop visits, which resulted in 45% less MRO spending. Even though this decision alleviated them financially, it also created a significant pent-up demand for MRO engine shop visits.
Accelerated adoption of new-generation aircrafts
During the height of the initial coronavirus wave, airlines grounded approximately 60% of their global fleet. Never before had the industry experienced such a large-scale suspension of its aircrafts. This industry slump accelerated airlines' pre-existing plans to retire their older aircrafts and replace them with newer models equipped with new-generation engines, such as CFM International LEAP and Pratt&Whitney GTF engines.
Although replacing older aircrafts with more efficient models aligns with the aviation industry's increasing sustainability goals, these new-generation engines require more repairs than initially anticipated, due to various issues, including powder metal contamination.
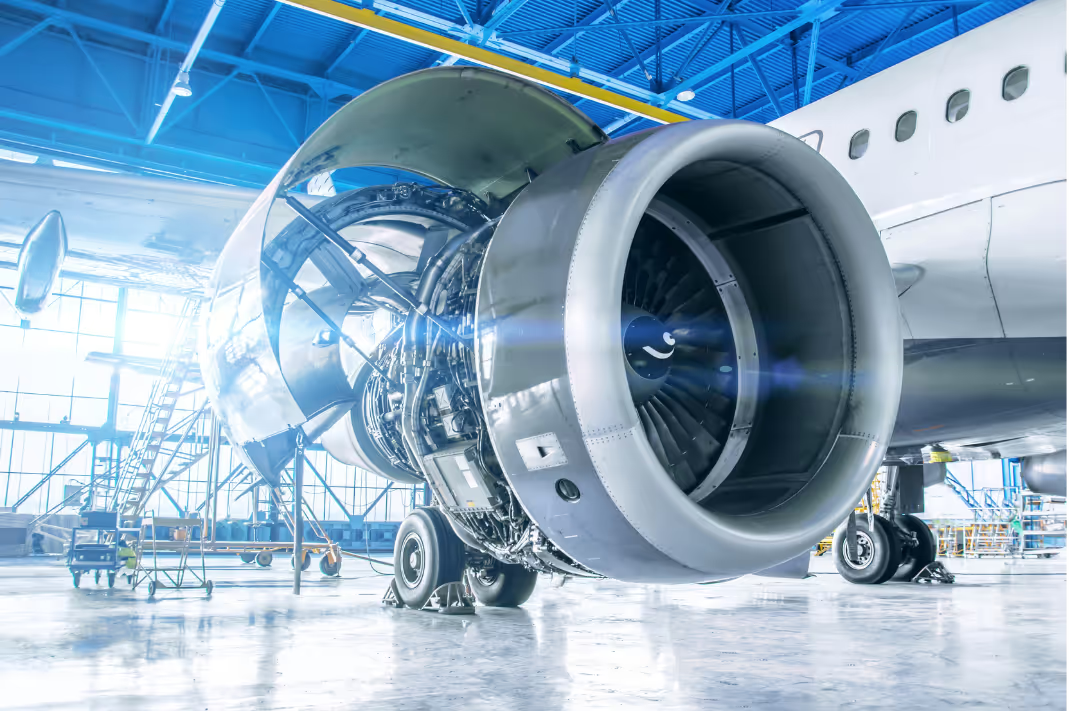
Continued reliance on aging fleets
Unfortunately, due to supply chain constraints and quality setbacks, the industry is currently seeing insufficient deliveries of new generation aircrafts. This reality was further intensified with airlines’ inflated demand for them, driven by the accelerated desire to retire older, parked, models (as mentioned above).
The continued dependence on aging fleets has had several cascading effects for MRO shops, all contributing to longer turnaround times (TaTs):
- Older aircraft models tend to require more frequent servicing, in addition to it being more complex.
- The supply of used parts is being strained due to delays in retiring legacy aircrafts. Used Serviceable Materials (USM) play a critical role as a cost-effective, low-risk option for sourcing life-limited parts. For some MRO shops, USM parts account for as much as 30% of total parts demand.
All these factors are converging to create a perfect storm. The result? MRO engine shop turnaround times are at a record-high: up by more than 35% for legacy engines, and more than 150% for new-generation ones, compared to pre-pandemic levels. Airlines are also experiencing TaT delays of up to 60-120 days, and the wait time just to secure an MRO slot has risen by 60-180 days. In addition, many airlines have been forced to cancel numerous routes and flights, resulting in lost revenue opportunities.
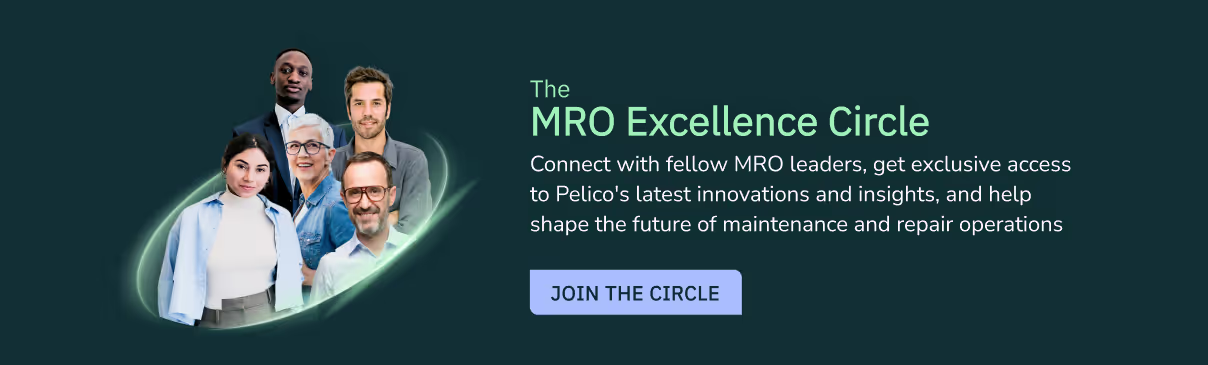
Act now: Be two steps ahead of the capacity crunch
With the quickly declining capacity and an imminent peak in demand, MRO shops that invest now in bringing agility and efficiency to their operations will be better positioned for sustained growth in the long run.
However, current factory tools do not provide real-time and actionable insights to quickly anticipate which parts will delay the kitting process. This leaves MRO teams in a firefighting mode, where up to 70% of their time is wasted manually aggregating multi-level BOM data from multiple sources in order to identify bottlenecks and the critical path. This results in delays costing up to $10k per day per engine and erodes customer satisfaction.
That's why our solution is designed to help you effectively manage MRO engine shop operations with the most comprehensive and efficient tools available."
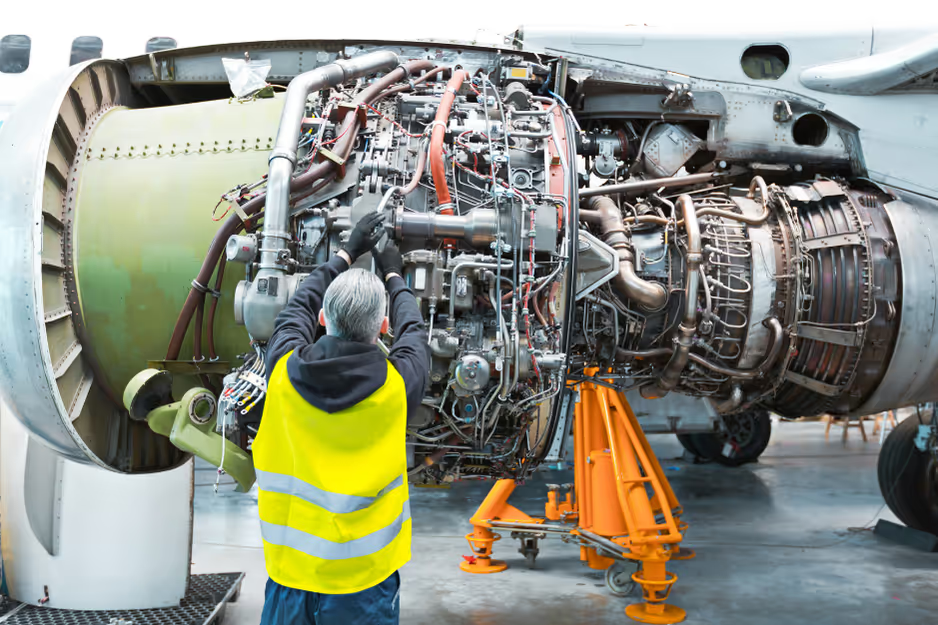
This is the reason why we, at Pelico, have been focused on building a comprehensive solution that helps MRO professionals efficiently manage their engine shop operations, from end-to-end. By using Pelico's MRO solution for aircraft engines, shops will be able to significantly reduce TaT, which will allow them to address the impending capacity crunch and surge in demand. To do so, our solution enables users to easily attain the following objectives:
- Boost customer OTD by quickly identifying the critical path and aligning the maintenance network with it
- Ensure material coverage at the kitting gate by proactively addressing shortages and enhancing supply chain visibility
- Improve engine throughput by streamlining repair planning under material and capacity constraints
- Make strategic resource allocation decisions by effectively prioritizing between OEM & MRO needs (for companies who manufacture and service aircraft engines)
A comprehensive MRO solution for aircraft engines
After many months of detail-oriented hard work, and close collaboration with 2 global industry leaders, we are happy to announce that Pelico's supply chain operations management platform now provides a solution for MRO aircraft engine shops.
And, the numbers speak for themselves: both of our industry-leading customers are already seeing proven results:
- - 40% TaT
- +94% Throughput
- +72% Team productivity
How Pelico's MRO solution works
In order to achieve these results, our MRO aircraft engine solution is built on 4 key pillars:
Data Synchronization
All MRO operations data is synchronized in one single place. This helps MRO managers ensure that the right parts are at the kitting gate on time, while at the same time having the ability to proactively identify the critical path using a comprehensive GANTT chart of the end-to-end MRO shop visit.
Bottleneck Anticipation
MRO managers can easily drill down into an engine's multi-level BOM to gain complete visibility on blockers (such as parts shortages, quality issues, late repairs, or subcontractor delays) and uncover their root cause.
Intelligent Assistance
Users have an out-of-the-box 360° view of all alternative stock opportunities and availabilities, and can make the right trade-offs by simulating alternative scenarios (based on material, capacity, and administrative constraints).
Cross-Team Collaboration
We believe all team members involved in the MRO process should be aligned and take coordinated actions, which will create an accelerated feedback loop that drives informed decision-making. In order to do so, Pelico's MRO engine solution enables real-time and contextual collaboration across all gates and functions, in one single platform.
So now, the only question left to answer is: what are you waiting for to transform your journey to resilient and efficient MRO operations?