Welcome to the World of Operational Intelligence
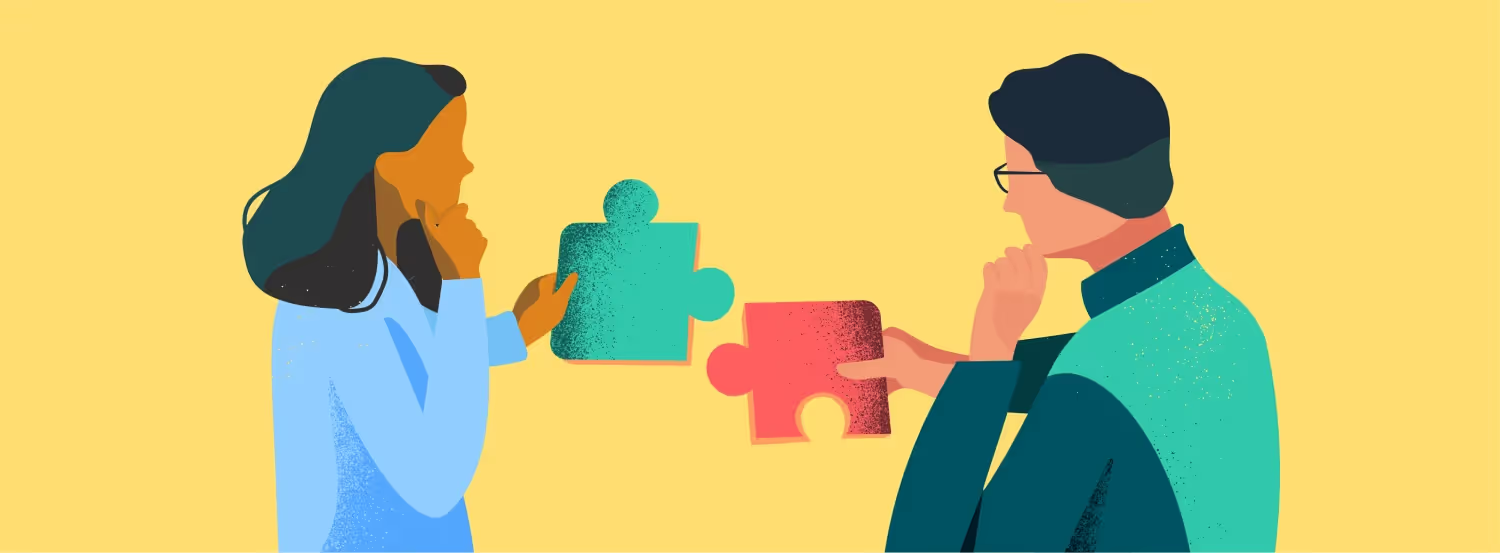
"We have petabytes of data and we’re doing nothing with it", a plant manager recently told us.
This is hardly a one-off case. In fact, the manufacturing industry is notorious for being data-rich but information-poor. Quality data, lead times of various operations, supply chain movements, etc… The huge data sets that plants produce daily are usually under-exploited or even wholly untapped.
When properly exploited, data and AI are opening up the opportunity to move from reactive to proactive operation management by cutting through the fog of uncertainty. And that changes everything.
Industrial Operations: a Data Management Problem
To check whether they are making the most out of their data, manufacturers can ask themselves three questions:
- Is the whole organization aligned on the same goals?
- Is operational effort consistently focused on those goals?
- Are operational teams making optimal decisions?
More often than not, the answer would be "no". Most plants use a collection of transactional systems, such as ERPs, PLMs, or CRMs, to support their processes but lack a common, centralized data repository to connect the dots. Accordingly, information silos and asymmetries between production, Supply Chain, Maintenance, and Quality teams prevent them from working in unison. Each team is blind to the challenges and requirements of others and pursuing its own priorities. Supply Chain managers order parts and equipment without knowing with certainty when they will actually be needed. Maintenance teams schedule operations on critical machines without factoring in the production timeline. And so on.
The same information gaps are blocking the vision of workers on their own perimeters, preventing them from seeing what they should be focusing their daily effort on so as to ensure proper completion of work orders and timely delivery of customer and purchase orders.
Ensuring the availability of critical parts, machines, and high-skill workers, or checking whether an order will be completed in time for customer delivery typically require hours spent juggling between spreadsheets and between various systems: Time-Tracking tools, the Quality Management System, the Handling and Transportation System, the maintenance plan, and more. All that is just to understand what the priorities are. And then, determining the best course of action to respond to those priorities entails yet another round of time-consuming data gathering. All in all, workers waste 60% of their time collecting the information they need instead of actively working towards the plant's priorities.
It doesn't have to be that way. Not anymore. Intelligent data solutions can now provide flawless visibility at the plant level, eliminate the noise to highlight the real priorities, automatically pinpoint production blockers and risks, give insights into the causes and consequences, and recommend corrective actions — such as alternative planning or resource allocation scenarios— based on historical data and predictive modeling.
Below is an overview of the benefits when a manufacturer embraces Operational Intelligence.
1. Increased Planning Adherence
Critical production equipment requisitioned for maintenance operations without notice. Last-minute realization that key parts are missing or nonconforming, or that operations need to be redone to meet quality standards. Overallocation of high-skill workers who find themselves unable to fulfill multiple assignments across competing tasks. These all-too-common production blockers are the reasons why so many operational leaders in complex manufacturing setups consider themselves in constant firefighting mode. And they are all the symptoms of the same root cause: poor anticipation.
In fact, a towering majority of the unexpected blockers that get in the way of the production process could have been anticipated. As a rule of thumb, the information about resource availability, skills, maintenance schedules, purchase orders, and so on is stored in one or the other of the plant's transactional systems (ERP, HR management system, etc.). But, with the data being scattered and siloed, the knowledge is only available to production teams at the cost of significant and painful effort. And, as the data is plethoric, pinpointing the most pressing issues, the most urgent tasks to be performed, is like finding the proverbial needle in the proverbial haystack.
What if operational teams could get a bird's eye view of cross-functional data with intelligent capabilities to predict issues and bottlenecks, detect potential scheduling or resource conflicts, perform ongoing assessments of the risks that might arise and derail production, and output recommendations for action? An Operational Intelligence solution combines planning data, delivery schedules, inventory, engineering configurations, work orders, purchase orders, and quality data into one place. Operators find the information they need at the push of a button. Moreover, algorithms automatically highlight the specific points of attention they should focus on and provide prioritized lists of actions and recommendations to mitigate issues. A worker with critical, unique welding skills is required to self-isolate because of suspected COVID-19 contamination? You are instantly notified, and the system suggests revisions to the production plan to push back the welding operation to a later time.
Because they are aware of roadblocks ahead of time, production managers and workers no longer have to respond urgently; they can prevent or mitigate them proactively.
2. Supply Chain Optimization
Information asymmetry between the supply chain and operations teams casts a cloud of uncertainty over production plans. On the one hand, Production teams have virtually no means to ensure they will get the right parts at the right time and in adequate quantities. On the other hand, supply chain managers typically juggle countless purchase orders. Due to a lack of insights into the priorities of production lines, they cannot focus their effort on the most urgent ones. Incomplete or outdated information on production timelines also impairs their ability to fine-tune delivery schedules.
Operational Intelligence will provide Supply Chain teams with comprehensive visibility and focused insights into operational plans to help them attune to the actual needs of production lines. The system will automatically let them know which of the missing parts are most crucially needed to address the priorities at the plant level, enabling them to take timely action. Because they enjoy perfect visibility into the production plan, they can optimally schedule the flow of inbound supply, thereby reducing the inventory cost and freeing up cash flow.
3. Shorter Cycle Times for Faster Delivery
When managing a complex production line or a mixed-model assembly line, one of the conundrums is to synchronize multiple operations with different process times. It is a matter of sequencing and arranging the flow of the tasks to be performed to avoid bottlenecks and minimize queueing and waiting times. In other words, it is about finding the shortest path to maximizing throughput over a given period of time.
Although the brave at heart can perform the calculations manually, any shift in the production chain will take them back to square one. With an Operational Intelligence system, an algorithm fed with all the relevant data computes the configuration that optimizes the overall process and determines the order in which the various operations should occur to minimize the overall cycle time.
4. Increased Efficiency of Human and Technical Resources
In a similar vein, limited resources — both workers and equipment — often have to be shared across tasks or production lines. Here again, the challenge is to identify the optimal distribution and sequencing model to minimize waiting times, increase the efficiency of each workstation, and improve the overall production system.
And, here again, data can help. It will use advanced algorithms to find and recommend the best scenario. It will help map out the optimal resource allocation plan and schedule work shifts to maximize resource utilization for improved efficiency — with a direct impact on operating costs.
5. Improved Visibility on Production Outputs for Improved Customer Satisfaction
Clients have their own agenda, schedules, and customers. They, too, need visibility into their supply chain. This is why ensuring customer satisfaction does not only require delivering high-quality products on time and within budget. It also hinges on a vendor's ability to provide instant and accurate status updates, to warn ahead of time in case of unavoidable delays, and to respond swiftly to potential order adjustment requests.
By empowering operators with data, Operational Intelligence enables them to align customer commitments with production priorities better. Additionally, with a clearer view of production end dates, they can provide clients with the reliable, accurate, and timely information they expect.
6. Deeper and Truer Insights for Continuous Improvement
One-time operations pertaining to specific issues and anomalies — for example, fixing an error on a costly critical piece — may require days and weeks of complex engineering calculations. Yet patterns tend to repeat themselves over time, making it possible to leverage the lessons learned from the past — as long as the information is readily available.
Operational Intelligence Solutions such as Factory Operations Management Platform will record all past calculations, decisions, and actions and consolidate the data into an "institutional memory" library, which can be readily accessed to accelerate the identification of recurring issues and replicate best practices. This way, instead of reinventing the wheel whenever the same situation presents itself, engineers save valuable time by replicating proven recipes and reducing non-quality costs.
Improved knowledge also means enhanced predictions. The actual (vs. expected) standard lead times of supplier delivery or operations, the scrap rate of a process: gaining a granular understanding of the actual level of performance requires frequently revisiting several constantly shifting variables. A Factory Operations Management Platform does it for you. It relies on data to enable you to monitor performance accurately, flag significant deviations, and better predict outputs.
Introducing Pelico
Pelico is a Factory Operations Management Platform designed to help operational teams in manufacturing cut through the fog of operational uncertainty.
We built it from the ground up to help operational teams cut through the fog of uncertainty and achieve predictable outputs. Basically, Pelico absorbs complexity and helps front line workers get instant visibility on their perimeters, anticipate issues, get AI-driven insights for smart prioritization and problem mitigation, as well as collaborate with other teams.
What’s our secret sauce?
Pelico acts as an intelligent layer that sits on top of transactional systems (ERP, PLM, Time Tracking…) and reconstitutes a digital twin for operations. Fueled by powerful algorithms, Pelico's factory operations management platform is collaborative and flexible. On top of its core platform services, it provides customizable apps addressing multiple use cases: Production Control, Supply Chain, Customer Support, and MRO.