Dissipating the fog of uncertainty to empower manufacturers
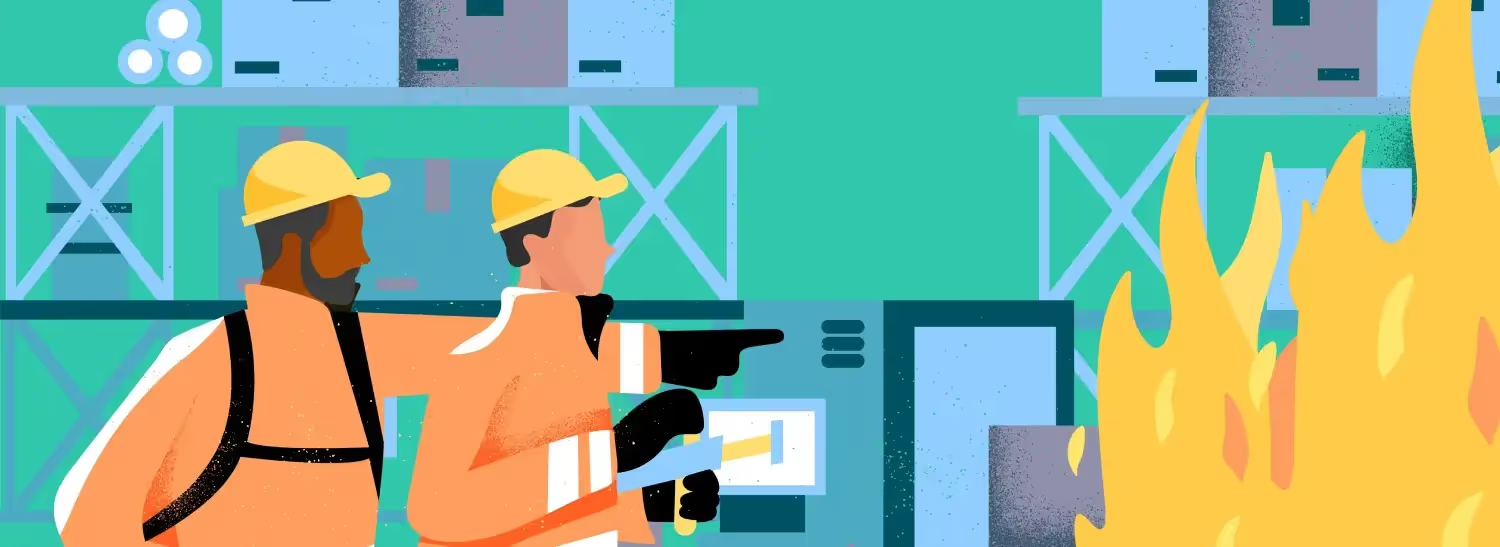
If anything can go wrong, it will.
Have you ever noticed how good old Murphy's law captures the essence of industrial operations?
For industrial production managers, problems and hurdles along the production chain are a fact of life. Manufacturers have been playing that game for a long time. Tracking down missing parts, solving resource allocation conflicts, making last-minute planning adjustments to address unexpected issues... Those are bread-and-butter concerns for operation controllers and supply chain managers across the industry. Making sub-optimal decisions often has snowball effects on costs, customer satisfaction, and team stress levels.
Great operations management can make the difference between extinction and prosperity.
But what happens when new players enter the field and play the game with new rules? As companies with a tech DNA, such as Apple or Tesla, engage in manufacturing. They leverage disruptive new technology to iron out all those wrinkles. This enables them to perform at superior speed and accuracy without even breaking a sweat.
- How can Tesla pass all regulatory requirements to produce the Model 3 in under a year when competitors take 4?
- How can Apple operate with 2 days of inventory when competitors need 1 month?
- How can players like Uber dynamically align supply and demand geographically and economically to guarantee their customers' cars in under 5 minutes?
It might sound like cheating… Yet it's not. Such technology capabilities are increasingly widespread and now available to more traditional manufacturers.
There is a growing performance and profitability gap between established manufacturers and new players, and the cost of inaction is too high.
Established manufacturers are now at an inflection point; they can either embrace the new possibilities of technology or stick to the old ways and possibly risk perishing.
Unnecessary Firefighting
One could say that the essence of industrial operations is the management of complexity.
Let’s consider a practical, real-life example.
A critical resource — such as a test bench — turns out to be unavailable to be used as planned. The domino effect will disrupt the whole production chain and may impact everything from production costs to delivery schedules. Unless you find a mitigation path and reschedule accordingly to alleviate impact.
But that requires visibility into the many moving parts involved in the production chain. In plants, operational data is usually scattered across siloed systems and multiple teams.
The information about schedules, quality issues, sourcing, machine, and skill availability is fragmented and requires manual reconciliation. When managing a complex assembly line, simply checking the status of a part may involve liaising with multiple teams and searching various databases. As a result of this lack of visibility, 60% of worker time is spent collecting contextual data to close information gaps.
Despite their best effort, teams usually need more real-time visibility on resources, schedules, budgets, inventory, and deliverables to optimally coordinate workflows, prioritize action, and work together in alignment.
Asymmetries of information across teams are the root cause of a number of inefficiencies.
It is too frequent for production teams to learn that a maintenance action is scheduled on their perimeter at the last minute. Too often are quality control teams looped in at the very end of the process, although they could have helped detect and fix issues at an earlier stage.
Long story short, the fog of uncertainty makes it hard to impossible to anticipate delays, conflicts, and blockers ahead of time to respond appropriately.
As a consequence, mitigation and trade-off decisions have to be made in urgency when unexpected problems arise. Typically, these decisions are relatively complex. For example, in case of a delay in supplier delivery, you need to assess the impact on the various facets of your production chain and, ultimately, your client delivery schedule. You need to determine the best mitigation strategy, evaluating different scenarios: Does it make sense to have an order split into multiple deliveries? Would the cost of investing in express shipping services be worth it?
Making such tough calls requires large amounts of input data and in-depth analysis to make the best choices. However, operators cannot afford to stall the process indefinitely while they comb databases in search of the correct data. So, they usually take shortcuts and make ad hoc, sub-optimal decisions in the moment's urgency.
Sounds familiar..?
Industrial operations are more complex and volatile than ever
Those long-standing problems have grown even more acute over the past years. The acceleration of the shift from mass-production models to more personalized delivery with lower volumes demands increased flexibility and agility in the production process. Faster-paced technology innovation and changing expectations of markets and consumers in the digital age combine to accelerate obsolescence and shorten product life cycles. Faster time-to-market has become a competitive imperative. This places further stress on industrial operations.
The introduction of enterprise IT platforms such as ERPs, CRMs, and PLMs has supported and streamlined targeted processes, but transactional systems are just not designed to assist end-users in decision-making and they were never designed for front-line workers. At the end of the day, the information that front line workers need in order to manage successfully is still fragmented.
As complexity increases, most industrial operators are feeling the headache. Says the manager of an Aerostructure plant in Toulouse, France:
My official job title may be Plant Manager but it really feels like I’m running a fire station. Putting out fires is what we do on a daily basis.
Most, but not all. New players from the Tech world have engaged in manufacturing operations, and they don’t seem to be feeling the complexity at all. Consider Tesla: they managed to pass all regulatory requirements for the production of Model 3 in just under one year, where traditional automakers may take up to four years.
What’s the secret?
Industrial operations is fundamentally a data management problem
Data. This is how new natively digital or digitally minded players are rewriting the book. Big data, analytics, predictive modeling, and AI-powered capabilities are the building blocks that enable the Teslas of this world to create smarter factories.
In this alternate reality, smart tools consolidate data to eliminate the need to search for information and provide a comprehensive view of operations. With predictive modeling and scenario simulation capabilities, production blockers can be anticipated ahead of time. And when problems do arise, increased visibility augmented by AI analytics and recommendations empowers operators to make informed and timely decisions.
The bottom line? Complex industrial processes are streamlined and sped up by orders of magnitude.
Take Amazon: with a catalog estimated at around 350m products— that is, over a hundred times more than the typical American supermarket — the E-commerce behemoth manages to commit to two-hour delivery where more traditional competitors struggle to achieve a 2-3-day delivery time.
A Tale of Two Worlds
In this new landscape, the competition appears to be rigged: regardless of their strengths, ingenuity and skills, traditional players can't keep up with such game-changing technology. While incumbent industry leaders are wasting time and resources putting out fires, the new digital challengers are leveraging efficiencies to gain momentum and improve market position. Data-enabled manufacturers are enjoying the cost reductions, productivity boost and higher margins that come with process optimization. The EBIT profitability gap is estimated at 30% and counting.
The performance leaps achieved by data-enabled manufacturers are ushering in a two-tier system. Ultimately, there will be winners and losers.
Pelico: Operational Intelligence for Smart and Collaborative Industrial Processes
Pelico’s goal is to empower operational teams cut through the fog of uncertain operations and achieve predictable outputs
Basically, our solution absorbs complexity. It helps front line workers get instant visibility on their perimeters, anticipate issues, get AI-driven insights for smart prioritization and problem mitigation, as well as collaborate with other teams.
We are a team of data experts from both the AI and Industrial Operations Management worlds. Former experiences with large manufacturers revealed a pattern of inefficiencies and performance gaps in the industry. So we created Pelico to bridge the gap between Tech companies and other manufacturers.
Our data solution is designed to meet the needs and challenges of the manufacturing industry in order to level up traditional industrial players and empower their knowledge workers with the latest advancements in Big Data & AI."
To give you a peek under the hood: Pelico acts as an intelligent layer that sits on top of transactional systems (ERP, PLM, Time Tracking…) and reconstitutes a digital twin for operations. An AI engine powers a collaborative and intelligent platform with core capabilities, as well as customizable operational intelligence apps to address multiple use cases such as Production Control, Supply Chain, MRO.
On average, our customers have recorded a 17% increase in planning adherence, a 40% reduction in missing parts, and a 15% jump in coverage rate of work orders.
That's the road ahead.